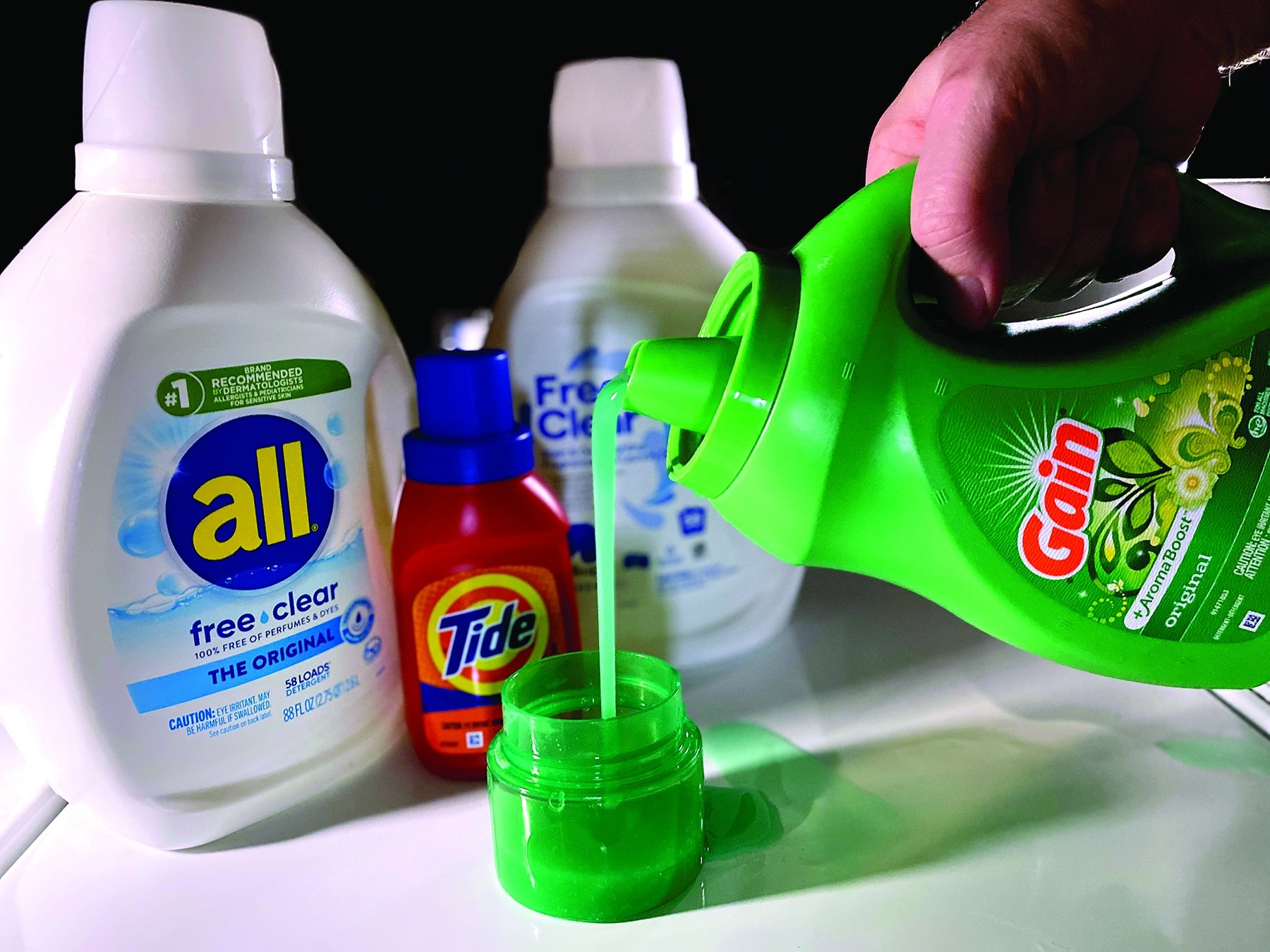
Detergents, Fluorescence and Photography
Brighteners work by absorbing ultraviolet energy and fluorescing or emitting visible blue-violet light. This effect can enhance the whiteness or brightness of materials.
All photos courtesy of the author. This article originally appeared in AC Jan. 2025.
The cinematographer has to think about a gazillion things on a daily basis. What special equipment do I need today? Which lenses? What color temperature do I want to shoot at?
One thing I’ve never thought about as I prepped for the day, however, is laundry soap.
This topic recently arose when I met with ASC associate member Tim Kang. When I arrived at Aputure, where he’s the principal engineer of imaging applications, he told me he was testing laundry soap.
It turns out this is something Tim has been investigating for two years on behalf of the ASC Motion Imaging Technology Council’s Lighting Committee, which he chairs.
So, what does laundry soap have to do with cinematography?
Bright Whites
As you know, manufacturers of laundry detergents compete for your business by making your clothes as “clean” as possible. This means bright whites. There are several methods they can use to get your whites brighter without resorting to bleach, which can damage some fabrics.
One is to slightly color the clothing blue, as white looks whiter when there’s a little blue in it. Another is to use optical brighteners, which are fluorescent pigments incorporated into the soap that become embedded in the clothing fibers.
The brighteners work by absorbing ultraviolet energy and fluorescing or emitting visible blue-violet light. This effect can enhance the whiteness or brightness of materials. These brighteners are designed to build up over time, so the effect is cumulative.
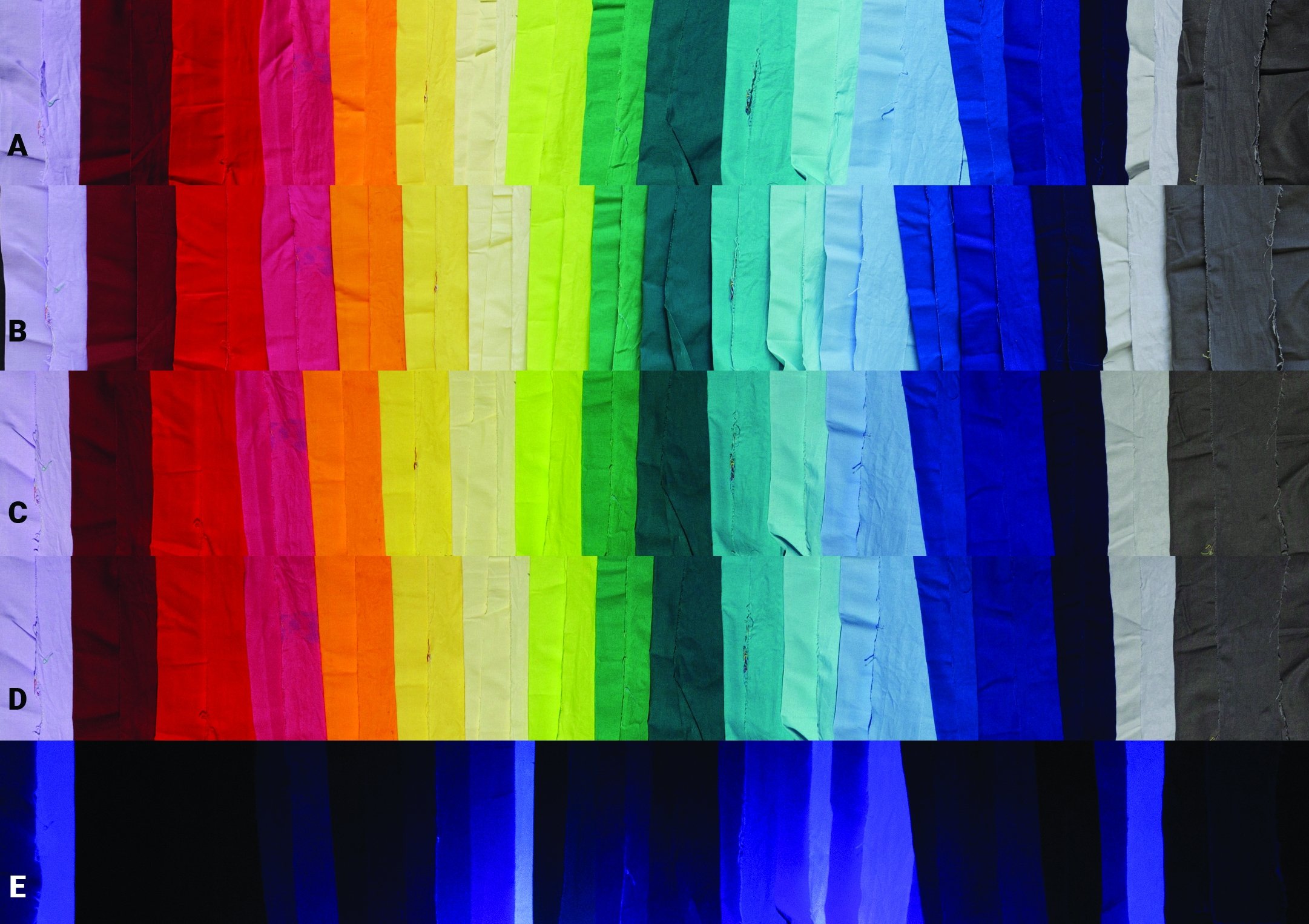
Here are some of the more common ingredient names for optical brighteners in laundry detergents:
• Disodium distyrylbiphenyl disulfonate
• Fluorescent brightener #71
• Fluorescent brightener 28 sodium salt
• Tinopal CBS-X
These kinds of chemical additives have been widely used in laundry detergent for the past 80 years or so, and while their environmental and health impacts are in debate, the issue at hand is the way they can affect your photography.
From the 1940s to the 2010s, the main sources of artificial light in film were carbon arc, tungsten and HMI, all of which have a relatively high concentration of UV energy, which reacts nicely with the fluorescent additives in optical brighteners.
Enter LED fixtures. LEDs, as discussed previously in Shot Craft, have a very limited bandwidth along the electromagnetic spectrum that is focused primarily in the 420-700 nanometer range — from violet-blue to red — and don’t extend to the shorter wavelengths of deep violet and into ultraviolet energy.
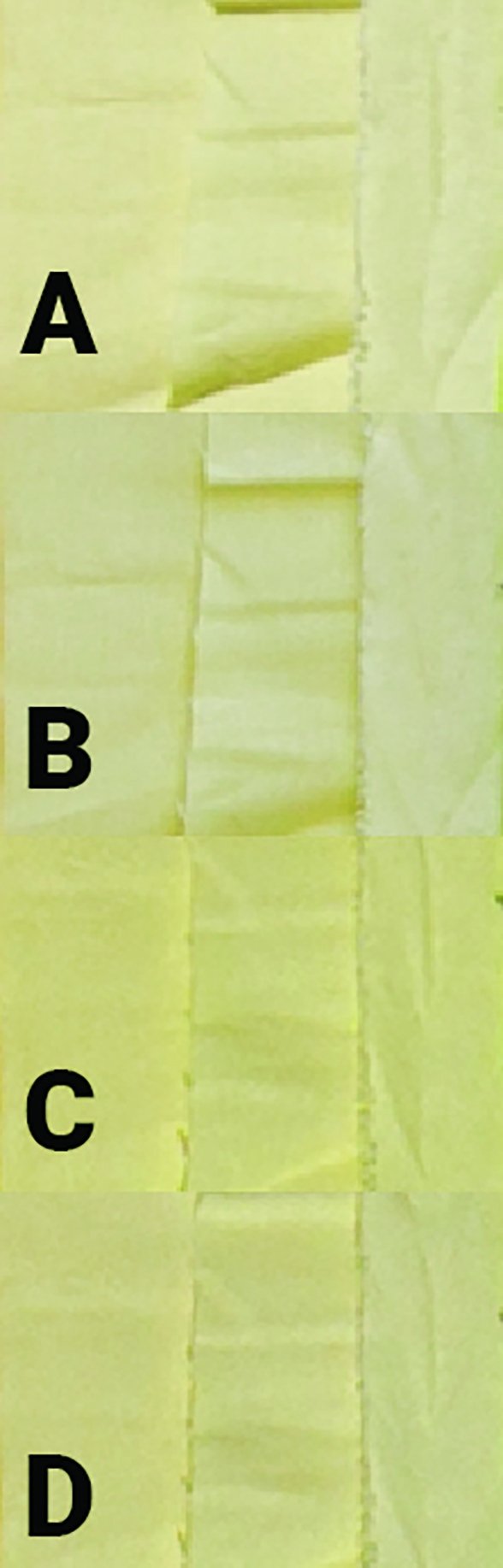
The UV Spectrum
On the electromagnetic spectrum, UV radiation falls between 100-400nm, and this covers: UVC (100-280nm), the most dangerous type of radiation possible for humans (and also the wavelength range used to kill bacteria and viruses); UVB (280-320nm), the wavelengths that cause sunburn and play a significant role in skin cancer; and UVA (320-400nm), the range mostly responsible for tanning and premature aging of skin. Consumer black lights typically emit 365-385nm, and bug zappers generally feature UV emissions around 350-370nm to attract insects that are drawn to UV rays. Of these wavelengths, those within 300-400nm induce fluorescence in certain materials.
Tungsten light was traditionally considered to have very little UV emission, but spectrometer readings on typical tungsten instruments show this is not the case — they often have emissions trailing off to below 400nm.
HMI fixtures are known to emit UVA and UVB wavelengths, and UV-blocking filtration is built into the fixtures’ safety glass (through which UVA is still emitted).
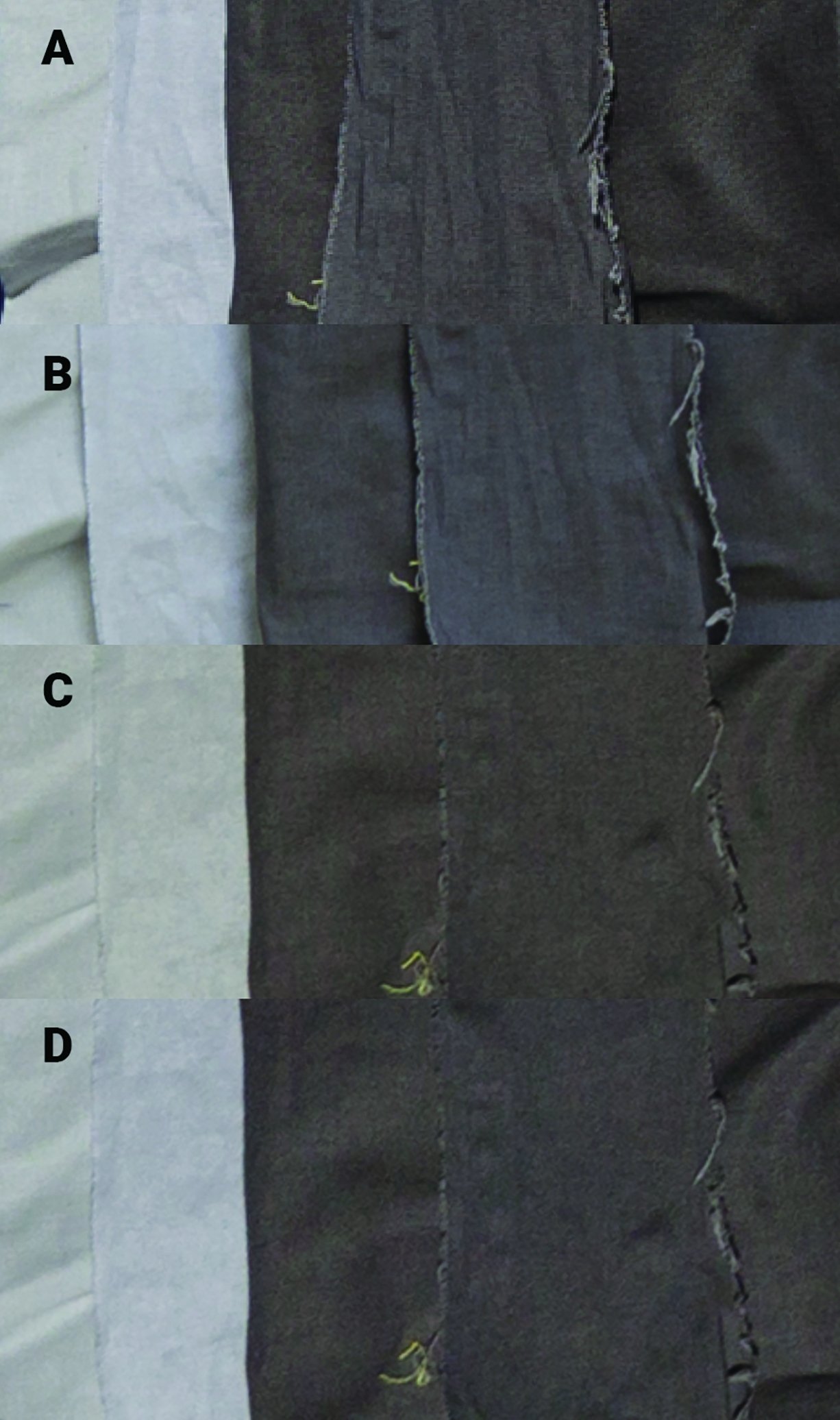
Today’s LEDs don’t really match natural daylight as much as we might like. Why is it that they don’t look quite right to so many of us? We know it’s about the color spectrum and color reproduction — and companies are scrambling to expand the spectral output with additional colored LEDs in amber, cyan, lime and so forth, generally at the cost of overall output. As more colors are added, the spectrum is filled out, but some brightness is lost.
We also know that color-fidelity measurement scales such as CRI, or even extended CRI, are insufficient to describe the effective color-spectral output of non-continuous sources like LEDs (see Shot Craft, AC Aug. ’17). Meanwhile, the Academy’s Spectral Similarity Index (SSI) seems to be one of the more accurate comparators for examining a reference spectrum (such as natural daylight) and that of a fixture, and very few fixtures rank above the 70 range on the SSI scale. (Because we’re accustomed to thinking of 100 as “the best,” many people assume an SSI of 70 is a “C” grade — when, in fact, they’re still excellent lights!)
But what if the spectrum could be slightly extended into a range that could not only better represent natural daylight, but could jump into the mid to high 80s on the SSI scale without loss of output?
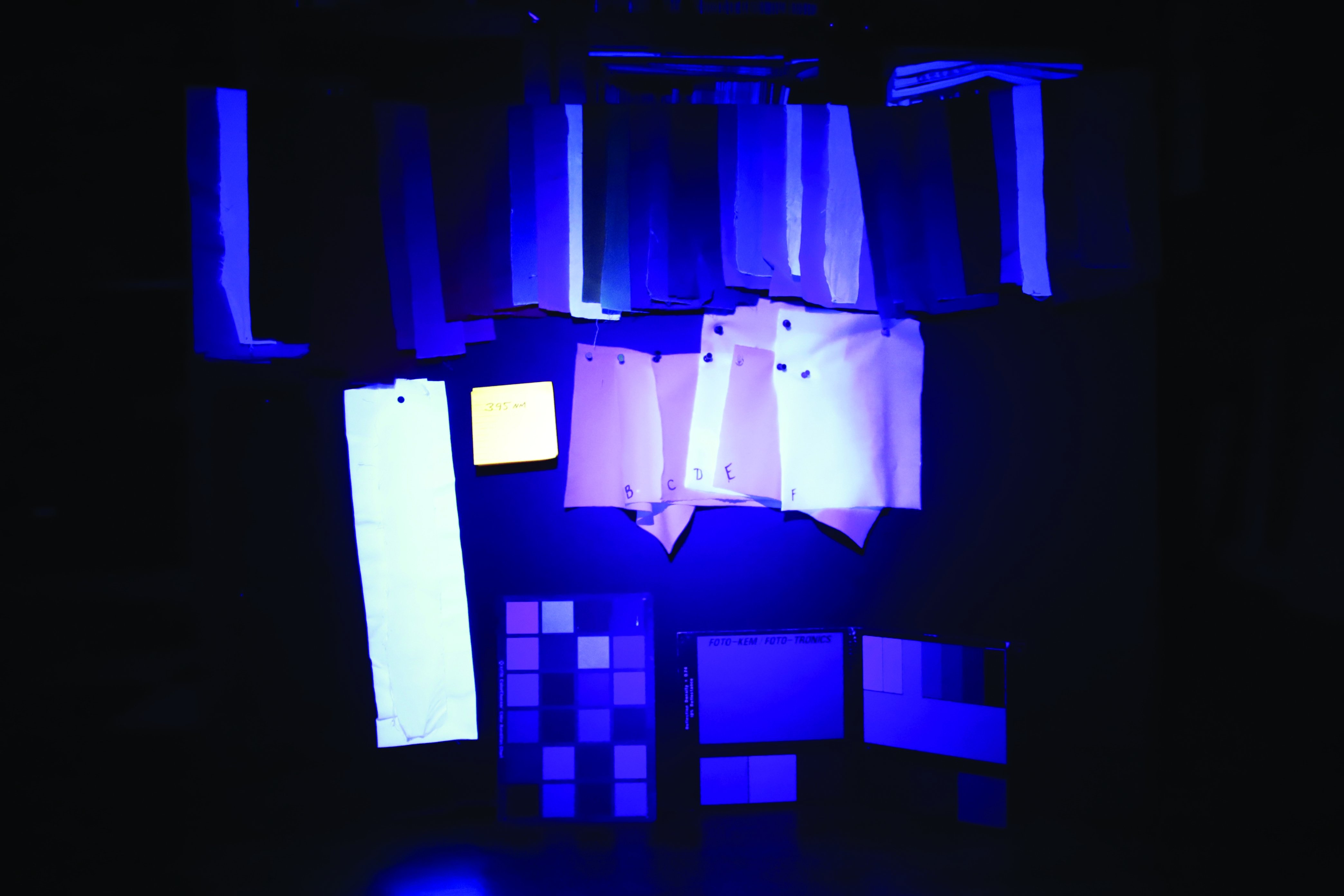
A New Method
At Aputure, Kang has introduced BLAIR (blue/lime/amber/indigo/red) color science — a “white” light fixture that includes UV emitters in the 400-430nm (indigo) range that do excite these fluorescent additives in clothing and, from what I’ve seen, also more closely emulate natural daylight. These wavelengths, while dipping into the UV spectrum, do not introduce additional health and safety concerns. In fact, they provide less longer-wavelength UV radiation than a typical tungsten light.
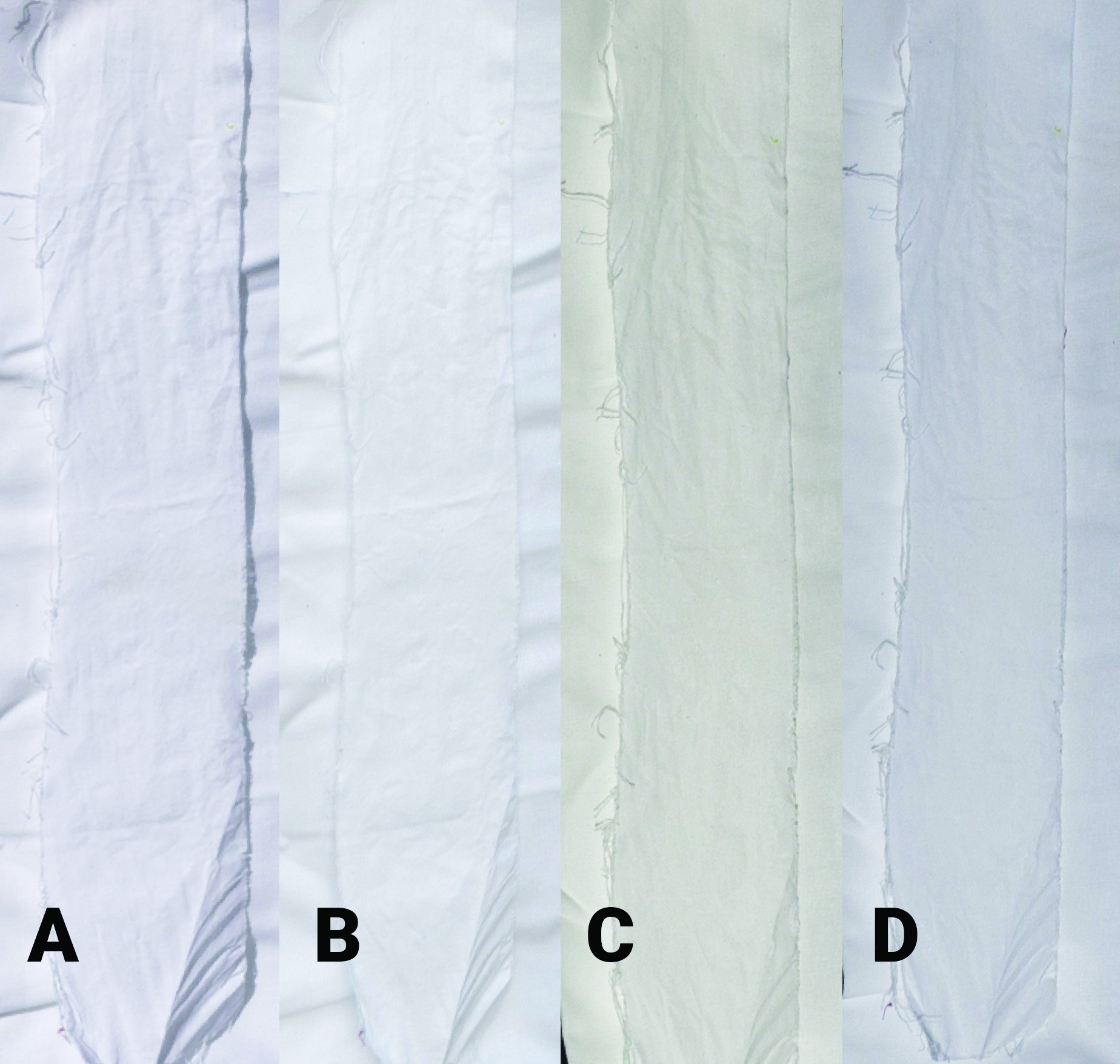
Aputure has no proprietary hold on the technology, which I hope means other companies will join the fray. When Kang showed me side-by-side examples of his laundry experiment, the most fascinating was a model wearing a white T-shirt that was treated with fluorescent-additive detergent, which was first lit with natural daylight, then lit to exacting quality and intensity from a current RGB Aputure fixture, and then lit with a prototype BLAIR fixture. The shirt with the RGB fixture looked slightly yellow, slightly dingy, yet it was cleaner white in the daylight and with the BLAIR fixture.
I decided to set up my own experiment. As some materials naturally fluoresce, and some have pigmentations embedded at the manufacturing stage, it turned out that the first cotton material I tried to test had its own fluorescence — which negated my experiment. So, on my next trip to the fabric store, I took a 395nm flashlight and checked all the materials to find low-fluorescing whites. I bought several types of such white material, which looked equally white to my eye. I also pulled 18 color swatches out of storage and cut off a strip of each to launder as well. To have a control, I had unwashed and washed examples in all cases.
After investigating laundry detergents, I selected four, each of which had a different fluorescent optical-brightener additive. I washed the different materials in the different detergents and set them all out for testing with natural daylight (both direct sun and open shade), with the Aputure 600c, and with the new 1000c Storm BLAIR fixture.
The results, while quite subtle, showed discernible — not massive — differences, primarily in the white material, and also in light yellow, cyan and even gray. The BLAIR fixture with the added UV wavelengths did reproduce these colors much closer to natural daylight, whereas the other RGB fixture did not. (I also found it fascinating that of the four detergents, two fluoresced at a “nuclear” level under 395nm light, whereas the other two fell flat — which also meant that the latter two had less of an improvement under the BLAIR light.)
Will this change your lighting choices? Maybe if you shoot a lot of product commercials or have a highly refined eye for color. But if adding these UV diodes improves color fidelity and does not compromise output or impact a fixture’s cost, why not? We’re all looking for better tools, better results and technology we can trust. This kind of innovation, while not necessarily groundbreaking, is a step in the right direction.