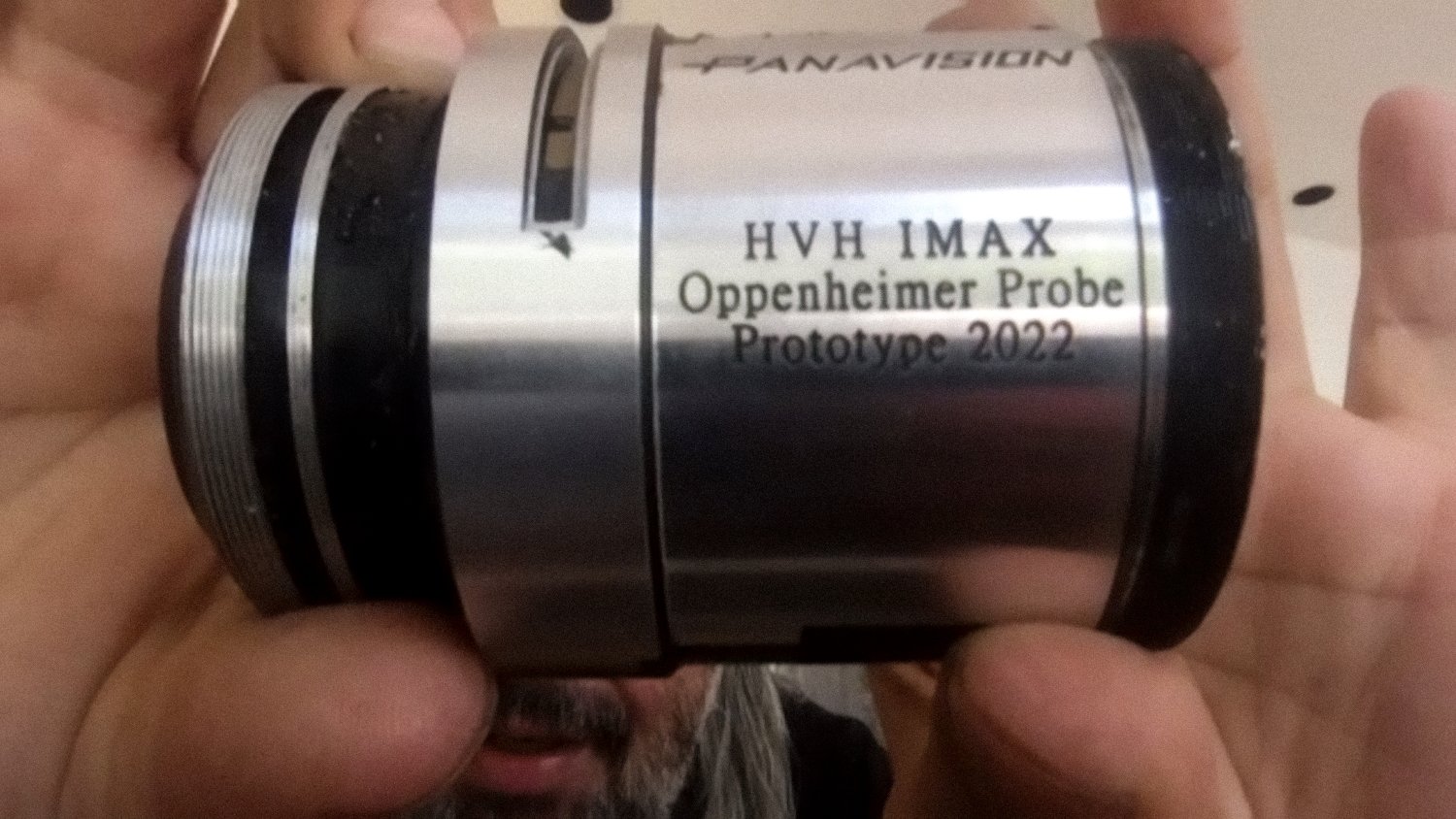
Creating Custom Optics for Oppenheimer
How ASC associate member and Panavision Senior Vice President of Optical Engineering and Lens Strategy Dan Sasaki designed an IMAX lens relay for the film's fascinating microphotography sequences.
This interview is part of American Cinematographer’s expanded coverage of Oppenheimer, photographed by Hoyte van Hoytema, ASC, FSF, NSC. A feature story with a special focus on lighting will appear in our October 2023 issue, and there will also be further web updates on other aspects of the production.
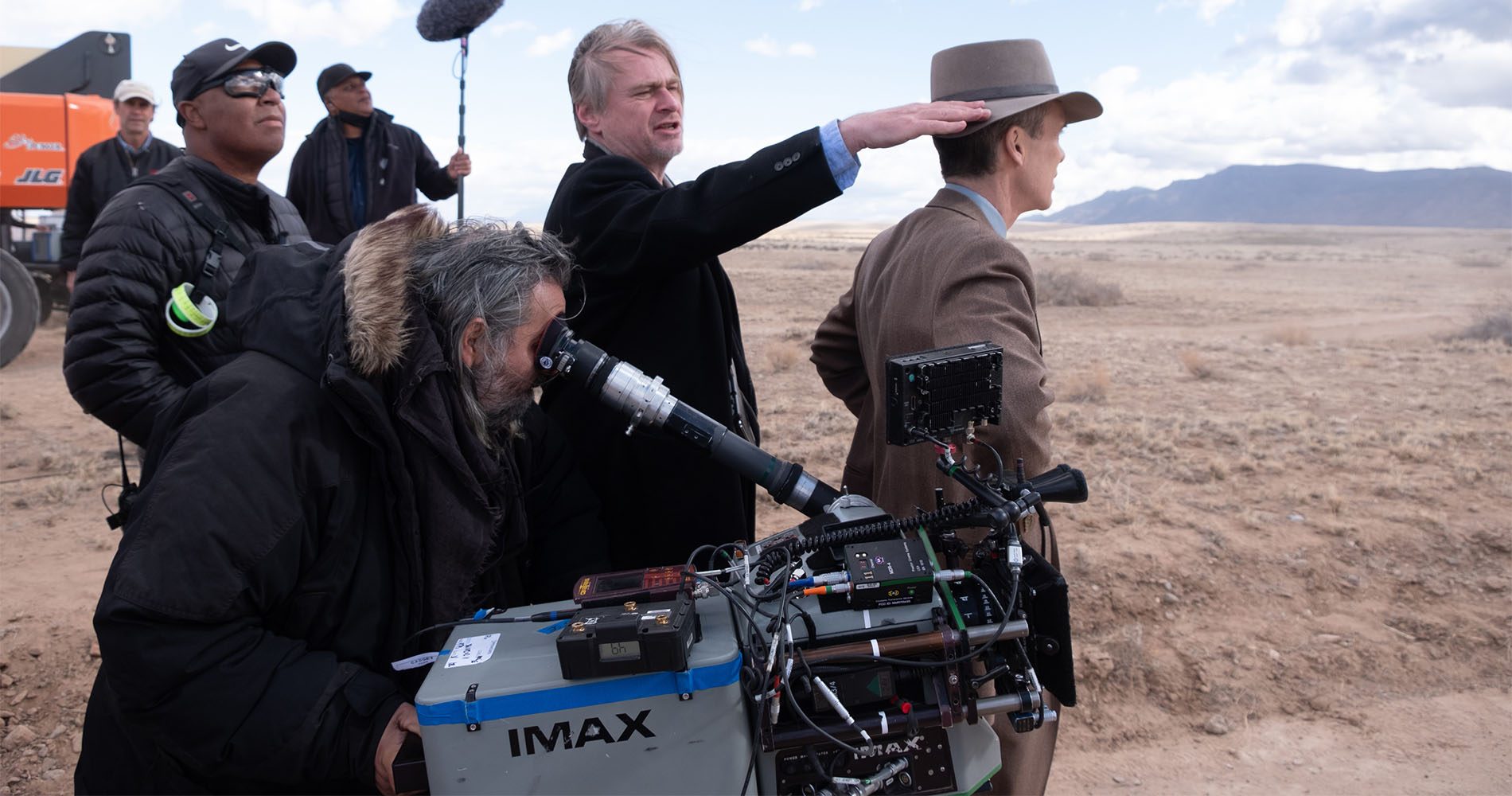
Throughout Christopher Nolan’s Oppenheimer, quantum physicist and father of the atomic bomb Robert Oppenheimer (Cillian Murphy) is plagued by visions of subatomic particles in motion and pulsating waves of pure energy. These fleeting visions strobe across the screen, shocking the audience with an indelible portrait of an invisible world.
Cinematographer Hoyte van Hoytema teamed up with special effects supervisor Scott Fisher (who has worked on all of Nolan’s films since Inception), visual effects supervisor Andrew Jackson (Tenet, Dunkirk), and visual effects director of photography David Drzewiecki (Tenet) to photograph submerged wood and aluminum flakes, burning thermite, and other microscopic elements in 15-perf IMAX as a means of representing Oppenheimer’s mental image of an atomic detonation.
Van Hoytema also called upon frequent collaborator, ASC associate member and Panavision Senior Vice President of Optical Engineering and Lens Strategy Dan Sasaki, to design a custom optical element — a 30" watertight, interchangeable IMAX lens relay — allowing the camera to literally enter a virtual world of colliding atoms and chain reactions.
In this conversation with AC, Sasaki talks about the perils and the payoffs of invention.
“I think of all the projects we’ve done with Hoyte, this one presented us with the most challenges.”
— Dan Sasaki
American Cinematographer: When Hoyte first approached you about this lens, what was he looking to achieve?
Dan Sasaki: He really couldn’t say what he was trying to do, because any project with Chris Nolan is generally very top-secret. All he said was that he wanted a waterproof probe lens that would focus very close, to cover whatever format we could. Then we said, “Well, what camera?” And he said, “Can you make it work for IMAX?” We told him it was going to be a challenge, but then I remembered we built large-format probes for the airplane cockpits in Dunkirk, so we started with that basic optical relay and modified it to be waterproof.
He started dropping little hints that they were photographing “particles.” So we said, “Oh, you want a microscope.” And he goes, “Yeah, a wide-angle microscope for IMAX.” We came up with a proof of concept for 65mm and IMAX cameras that was not even close to being waterproof, but it worked.
That led to the next iteration, with 35mm and 24mm equivalent objectives. We built the 35mm first, knowing that 24mm would be more difficult. After more testing, Hoyte asked us for closer focus and to make sure it can go at least nine inches below the water’s surface. Our next step was to make it waterproof and set the lens stops. Initially, they were testing the probe with a waterproof membrane in the side of the tank that limited the diameter of the relay, but because the depth of field was so shallow, he was working at deeper stops, which accommodated smaller glass elements and shrunk the size of the probe.
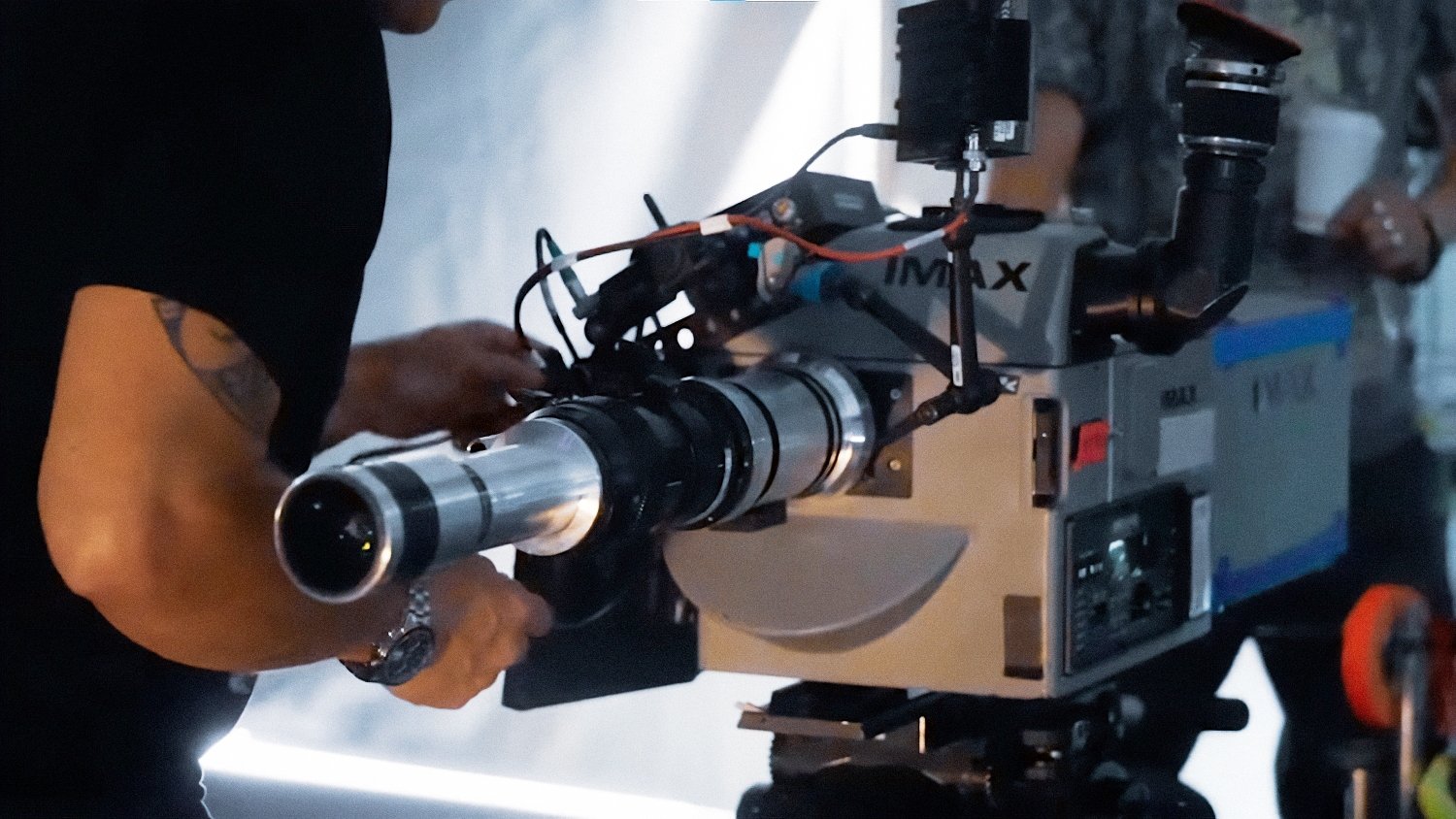
Hoyte and his team took the prototype and started shooting with it, and pretty soon I got a call from [first AC] Keith Davis about “a little disaster.” I thought maybe it started to leak water, which was no big deal. We can dry off the optics. But when we got the probe back, the entire front element was shattered. They’d been filming steel marbles spinning around on wires, got into the moment, kept pushing closer and closer, and Keith tried to warn them when all of a sudden they heard the wack-wack-wack of a marble hitting the front of the lens. In most circumstances that would have been a problem, but because this was a prototype, we just built another one, which actually came out a little bit better because we were learning from our mistakes.
Now, something that I had completely missed up to this point was that I’d been doing all of my testing above water, and air has a different refractive index [the ratio of the speed of light in a vacuum to a given medium; in this case, 1:1.0003] than water, which is denser [1:1.333], and this threw off the close focus. So we made an intermediate optical surface — the equivalent of a snorkel mask — with a little bit of [dioptric] power to separate the surface of the lens from the water and correct the issue.
The final surprise in our development was that during one of the tests, the probe — which we designed to be watertight for up to four hours, but not completely waterproof — was left submerged overnight. Water got into the relay assembly and completely wrecked the optics. After that, we sealed everything a bit better.
What was the close focus on that lens?
I believe the 24mm close focus is less than a millimeter inside the front element, and the 35mm is approximately ¾" beyond the front element, if memory serves.
Why was the 24mm objective more difficult to build than the 35mm?
I normally solve the vignetting issues associated with wider focal lengths by increasing the diameter of its elements. In the case of the probe, there was a maximum diameter constraint, which created vignetting issues with the first 24mm prototype. To meet the size restrictions as well as the performance requirements, the 24mm lens required five additional elements in a more compact optical design.
Do you magnify or modify the resolution of the image through the relay?
We basically copied what we did for Dunkirk’s cockpit relay, modifying its optics for the IMAX diagonal. Unlike Dunkirk, Hoyte wanted a little bit more personality to the lens, so instead of a perfectly flat field, we actually caused it to follow the shape of the spinning particles. But more importantly, we were taking a VistaVision-sized image from one end of the probe to cover a 15-perf IMAX frame, so we had to magnify it while preserving the resolution.
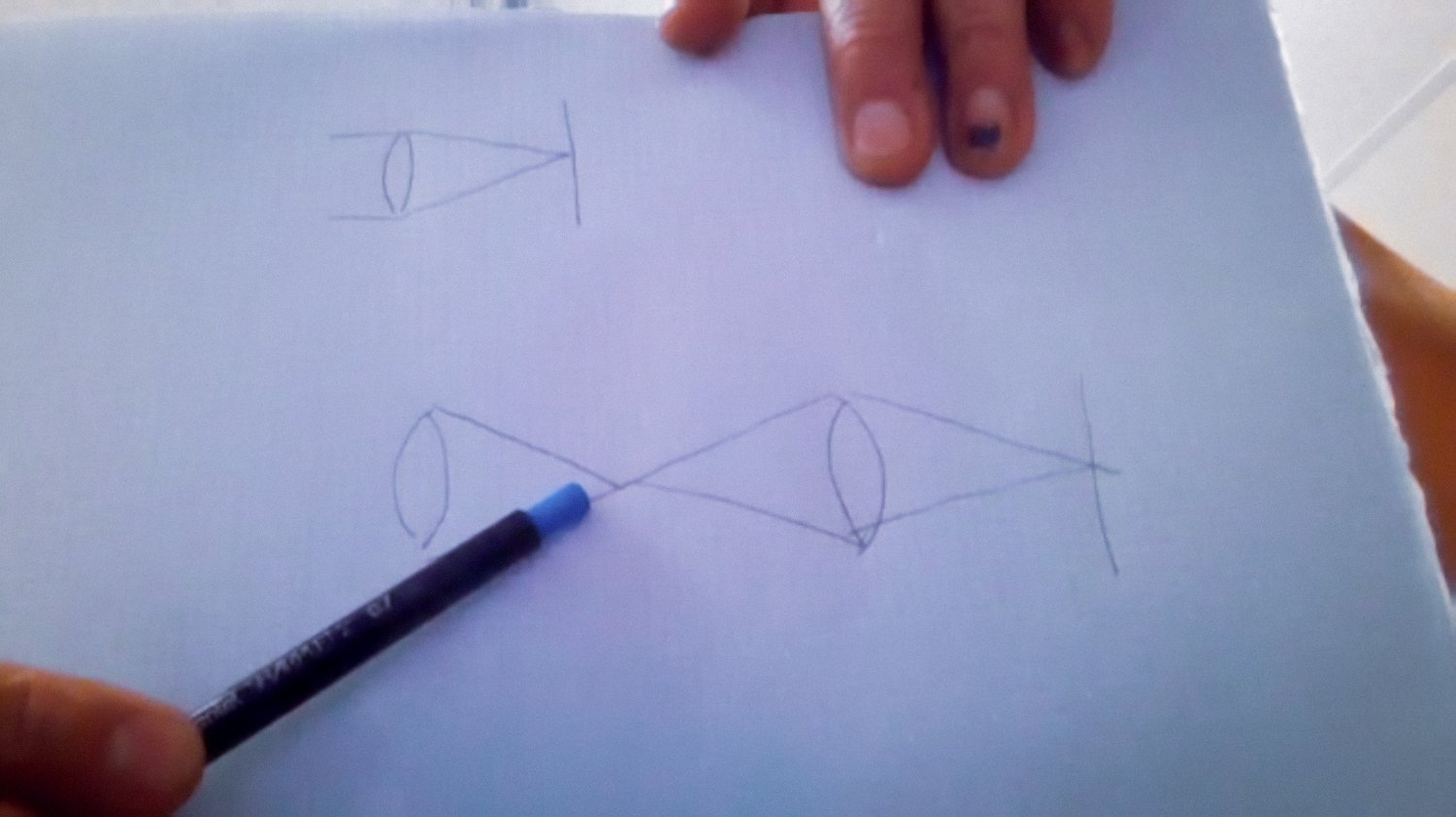
The first time we sent the relay out, I was under the impression it was just a macro lens, but what I learned later is that they actually wanted an extended object distance — not just right up against the lens, they wanted the ability to focus past it — so we had to extend the focus travel and change the way the lens functions to something more like a standard lens.
Where does it hit infinity?
We bracketed the sweet spot around 20', then at infinity we just let it do what it was going to do. Beyond that, you don’t have much focus travel so you have to rely more on hyperfocus.
What’s the ideal T-stop for these lenses?
The fastest the relay can go is about T/4.5, but it can stop down to T/32 if necessary.
Are T-stop adjustments made on the objective or the relay?
The T-stop was adjusted on the relay because it would have been difficult to keep the objective water proof if it were fitted with an adjustable iris ring, and it would have been almost impossible to adjust the T-stop while shooting underwater if the iris were on the objective. The same goes for focus.
Is the objective considered a separate or integral part of the relay?
Technically, the objectives are separate entities, but in reality both were built to complement the main relay tube. By making the two components work together, we were able to keep the performance more consistent across the image field.
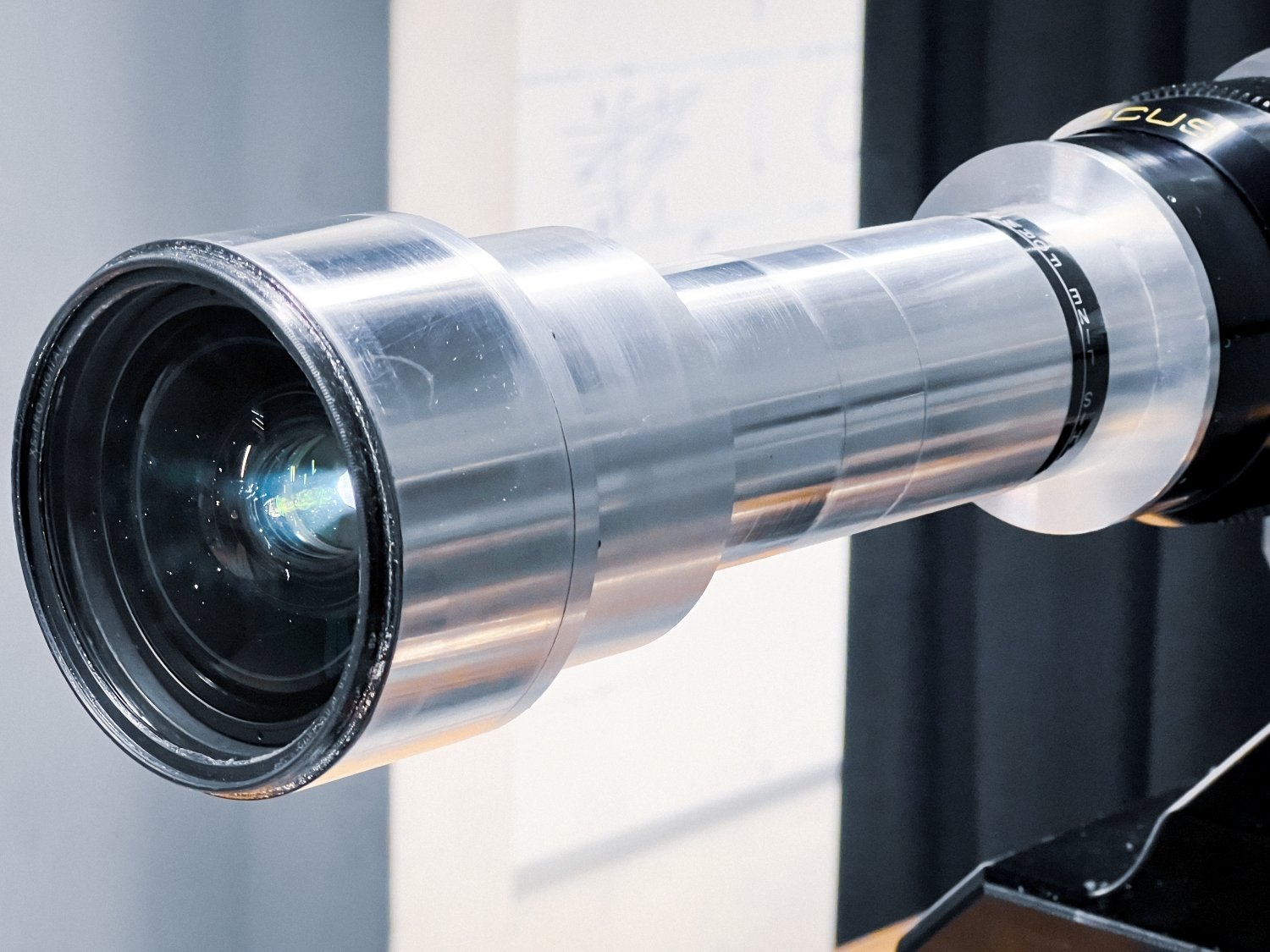
How many elements are between the objective and the image plane?
There are 25 elements in the relay, and the objective was maybe an additional 12 elements.
Is that a big ask for a custom lens design?
Not really. Hoyte is one of those people you’ll do anything for because every project he touches is amazing. He’s also technically astute — he has his own machine shop and he builds his own parts, so he’s very understanding of the process and gives us the lead time to do things right. He’s hands-on, so it’s not, “here’s what I want” and then comes back six months later. He gets involved. And Keith helps keep us grounded so that we’re making something usable, not just this block of glass.
Hoyte has at least one objective in his possession, but now that the relay is in Panavision’s repertoire, will it be available for other filmmakers to use?
Yes and no. Much of what we’ve developed in the past we’ve turned into product — the relays for Dunkirk were used for large format cameras on other productions — but in the case of the Oppenheimer probe, we don’t have any plans to release it right now. At least, we’ll wait until the movie’s out and Hoyte gets to talk about it. I don't want to undermine all the work that he did.
Is there anything else about this lens that AC readers would be interested in learning?
I think of all the projects we’ve done with Hoyte, this one presented us with the most challenges, just because of all the mishaps. It was always something — the water getting in, it got smashed, or we forgot to account for the refractive index differential. But because Hoyte and his team are so on top of things, it was ultimately successful.