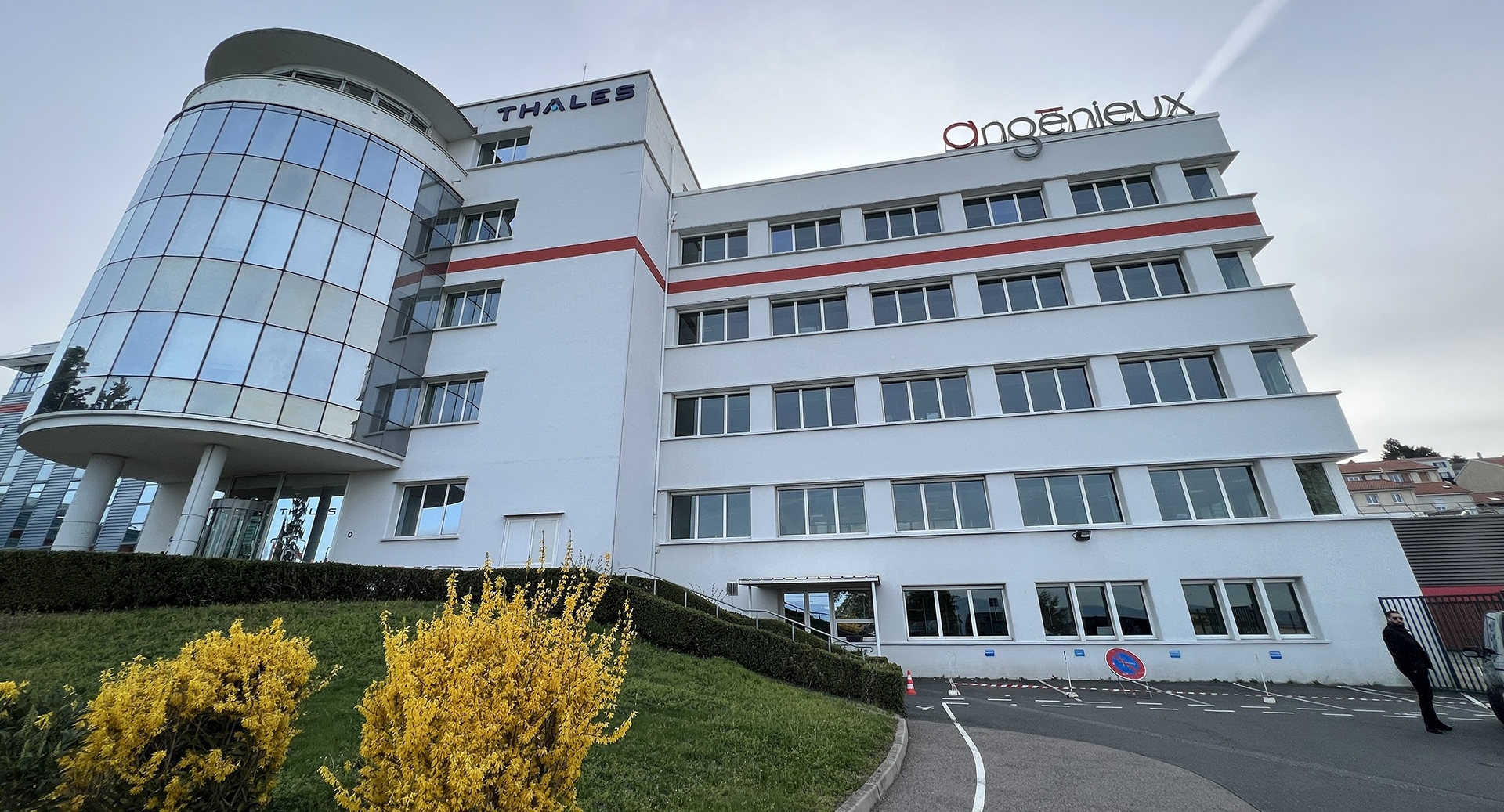
Angénieux Visit — A Photographic Reportage
An annotated photographic reportage of a visit to the company’s lens factory.
This is a photographic reportage — with some notes — of my visit to the Angénieux factory, where I was recently invited for a tour, along with three fellow journalists. A big thank you to the Angénieux team for their invitation, and their warm welcome. I took most of the photos below, but my friend Marc Salomon — Editor-in-Chief of the AFC Website — kindly let me include some of his as well, which are complemented by a few images from Angénieux, as indicated.
SAINT-HEAND
The Angénieux factory is located on the scenic heights of the town of Saint-Héand, in central France near Lyon.
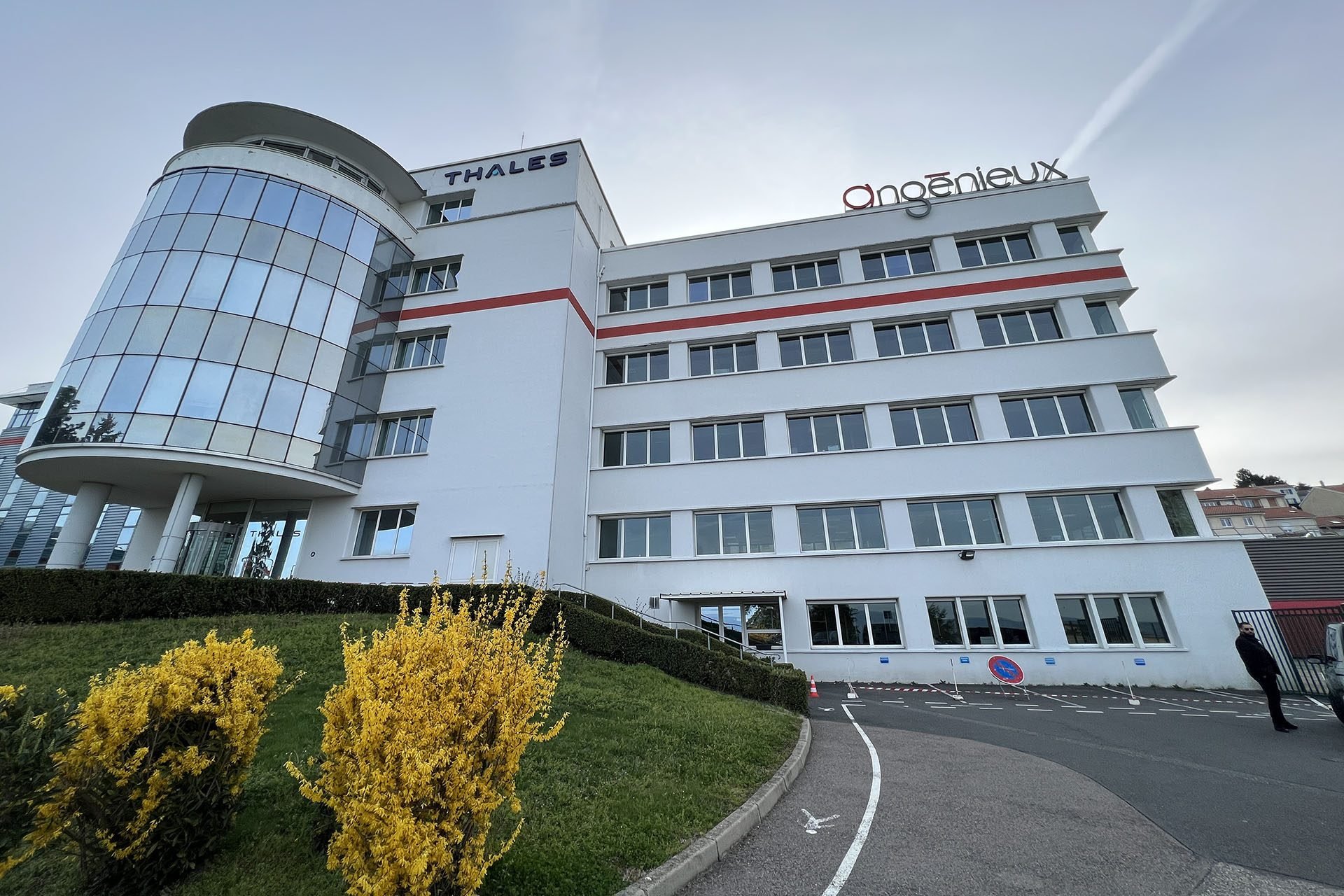
-- Fun fact: the building’s cylindrical tower on the left actually represents a zoom lens, Angénieux’ signature product.
-- Angénieux was acquired by the giant Thales group in 1994
THE GROUP
Here is the group of hosts and visitors:
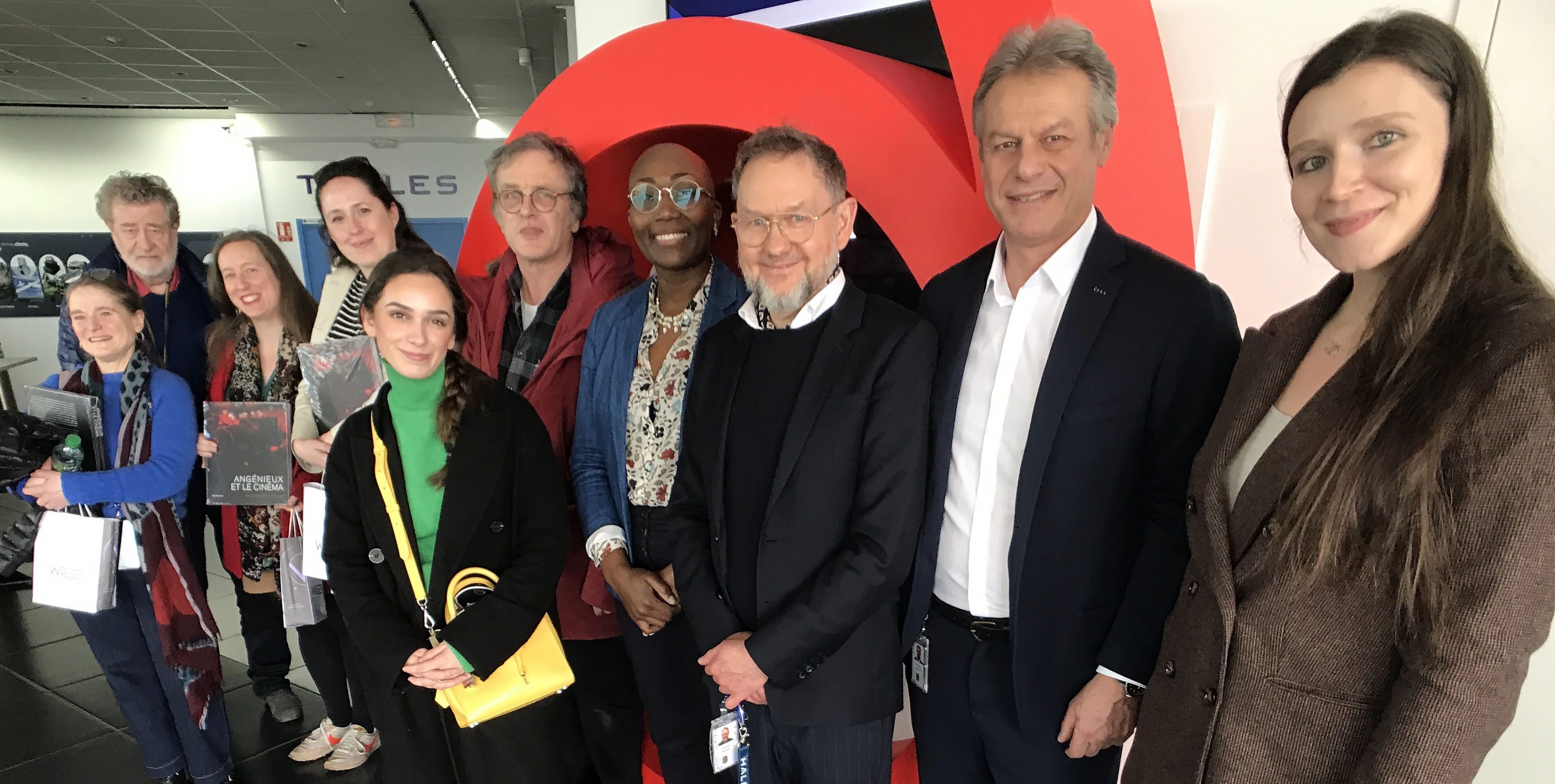
From right to left: (near to far):
Clara Fily, Content & Digital Manager, Thales
Christophe Remontet, Head of Zoom and Imaging Solutions, Thales
Dominique Rouchon, Deputy Managing Director, Angénieux International Sales-Marketing & Communication
Danielle Pitel Pambia, Head of Communications, Thales
Marc Salomon, Editor-in-Chief of the AFC Website
Fanny Modri, Communications Apprentice, Thales
Helen Parkinson, British Cinematographer magazine
Anne-Lise Kontz, publicist
Hubert Niogret, Positif magazine
Isabelle Buron, publicist
Not pictured is Eva Collin, Welcome Services Manager
OSCAR
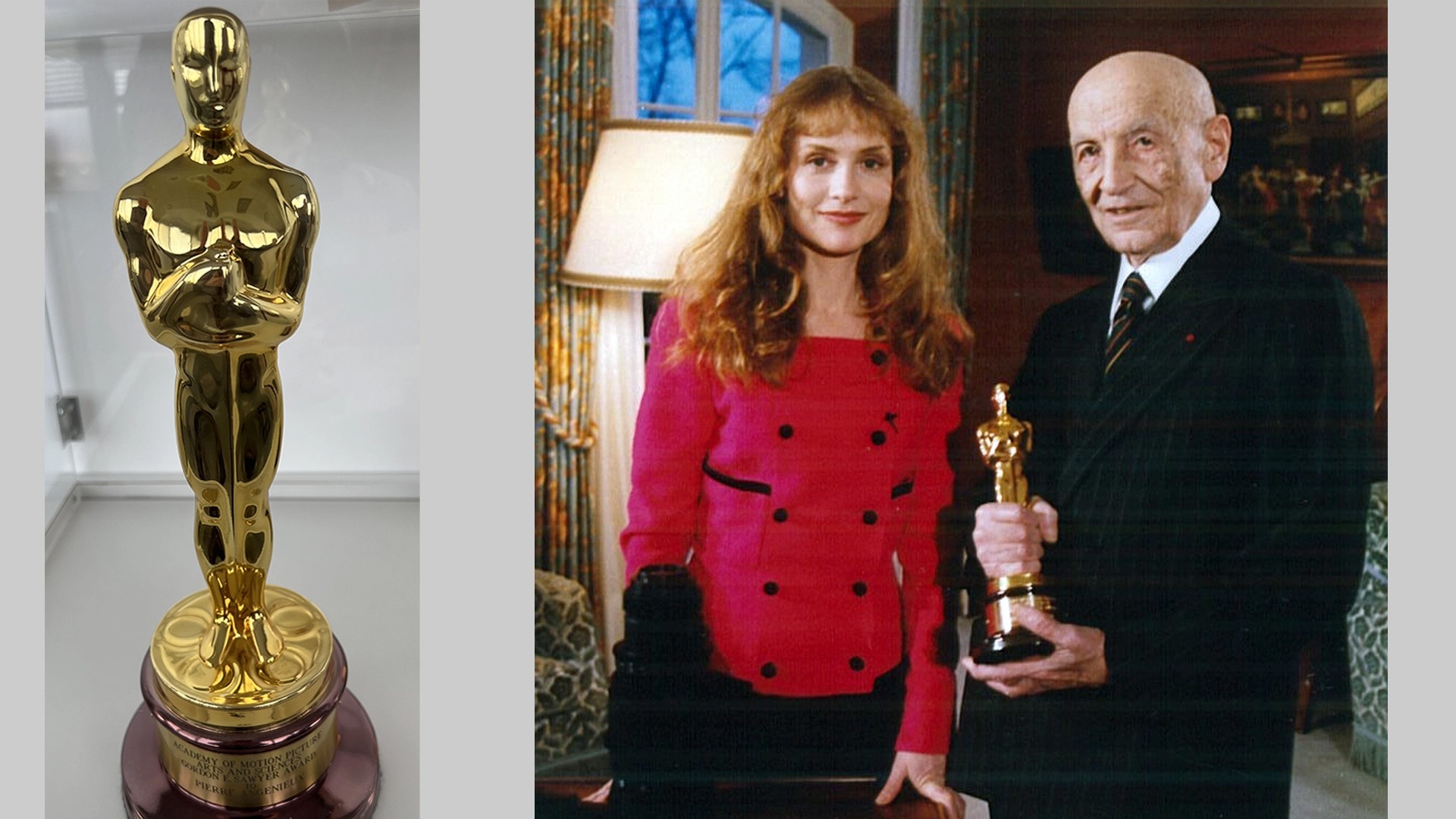
At the beginning of our tour, we enter a space full of awards that Angénieux has received for their lenses. For me, the most prestigious is the honorary Gordon E. Sawyer Oscar, presented to Pierre Angénieux by French star Isabelle Huppert in 1989. The late Monsieur Angénieux received this cinema technology award at the age of 83, rewarding a lifetime dedicated to the design and manufacture of zoom lenses at the company he founded in 1935.
INTRODUCTION
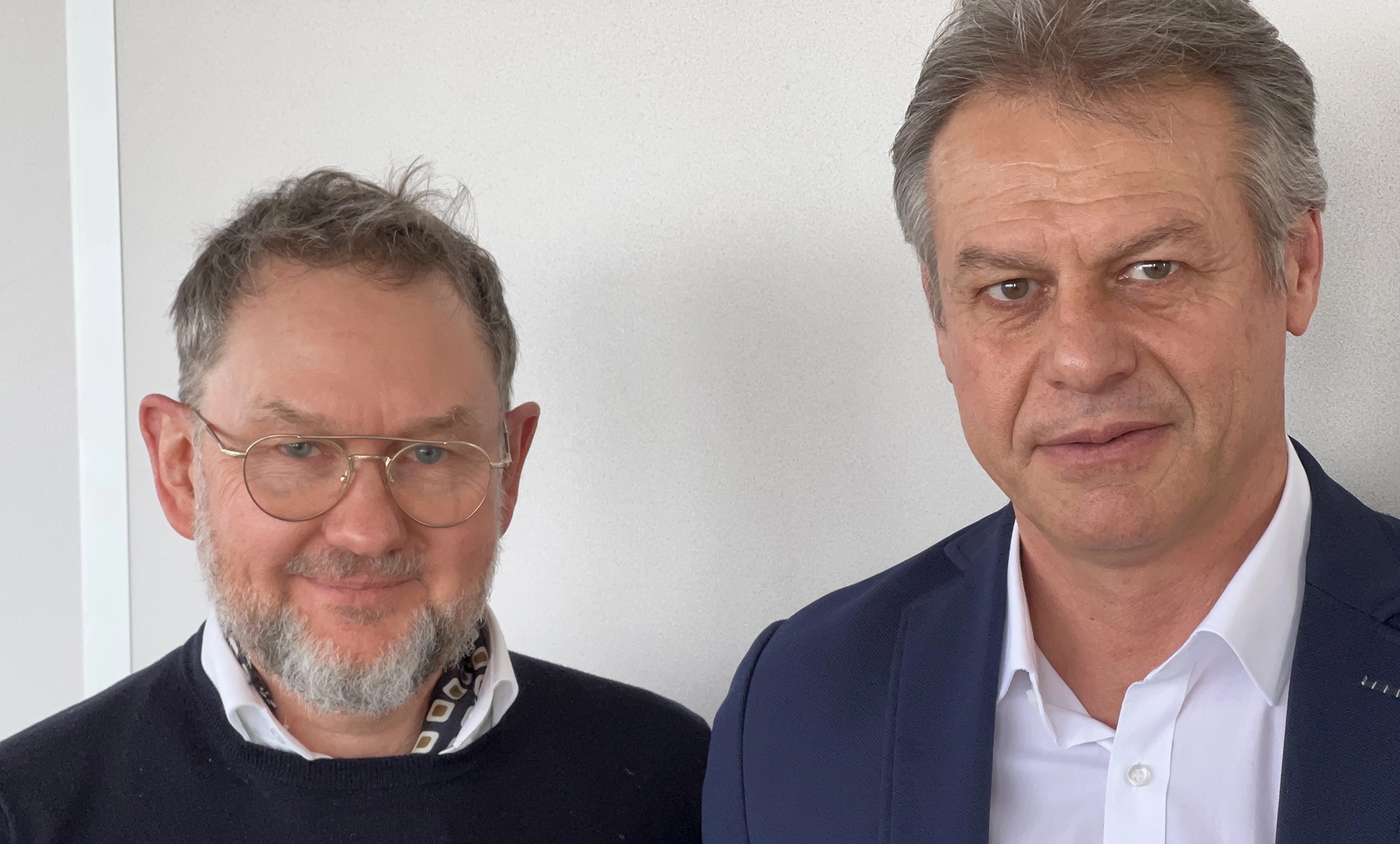
Our main hosts for the visit are Dominique Rouchon and Christophe Remontet.
They offer a brief introduction:
-- The site specializes in high quality zooms and primes for cinema, but also optics for other industries like avionics, medicine and defense (for example, night-vision goggles).
-- There are 350 employees on site, about 200 work on cinema products.
-- Half of the site is dedicated to manufacture. There is also a lot of R&D.
-- 70% of their sales are outside of France.
-- More than 1 million Angénieux lenses released in the world since the company’s inception.
-- Most of Angénieux' raw glass comes from Japan.
-- Angénieux sub-contracts some lens and mechanical elements, but the most complex lens elements are cut and polished on site, and so too with the most complex mechanical parts.
-- A theme both men express throughout the day is that Angénieux combines the highest level of technology and of craft, built by master craft people and technologists.
-- Dominique compares building Angénieux premium lenses to the precision and craft of haute couture.
-- A single lens, says Christophe, can require up to 350 hours of manufacturing labor.
TWO RECENT TECHNOLOGIES: IRO AND IOP
Christophe and Dominique present two key recent Angénieux technologies: IRO and IOP.
These topics are also covered in detail by my friend Jean-Yves Le Poulain, Angénieux Product Line Manager, who presents a hands-on session with Angénieux lenses at the end of our visit.
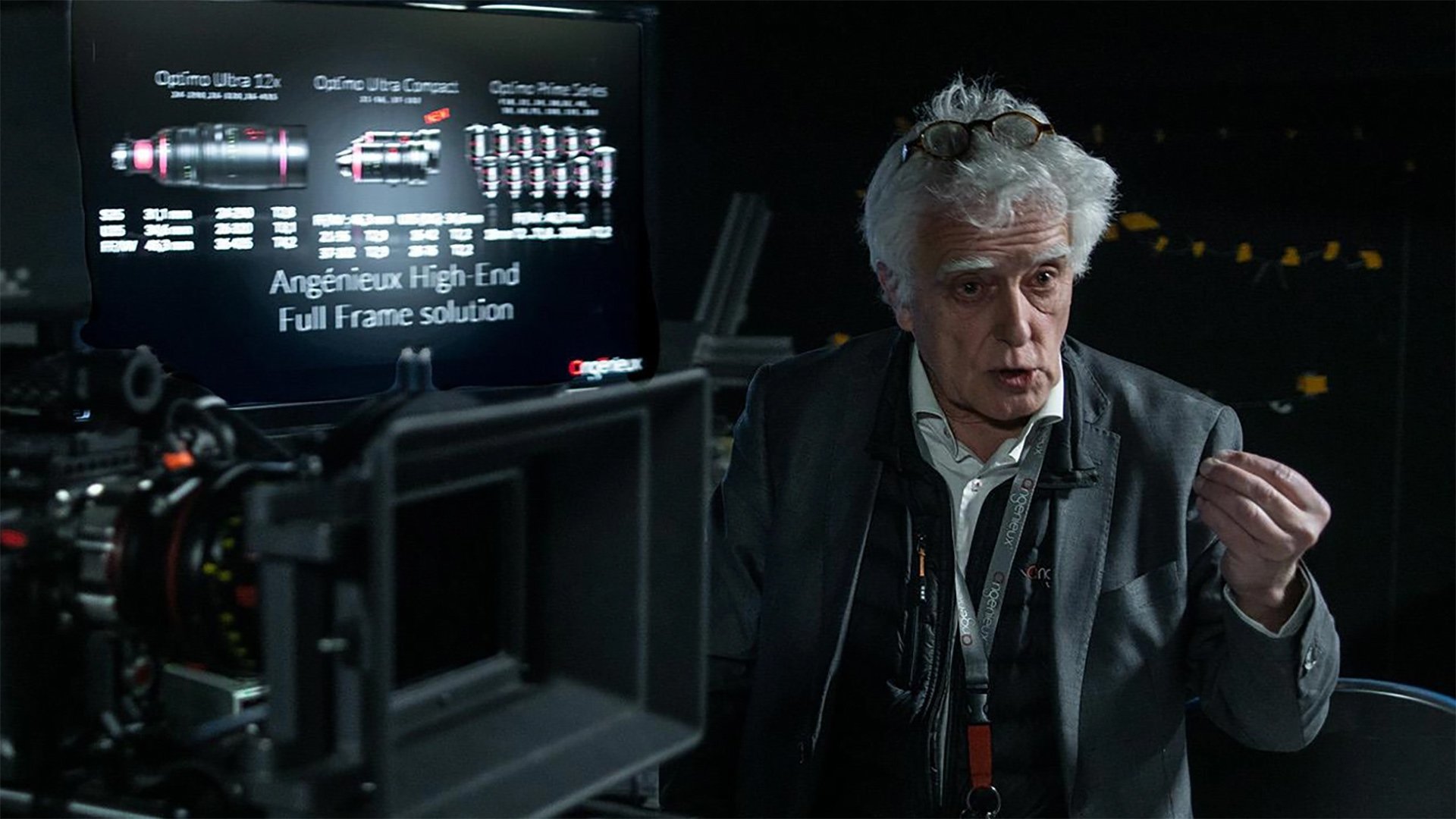
IRO = INTERCHANGEABLE REAR OPTICS
IRO allows for using the same lens for 3 different sensor format sizes (Super35, Open Gate and Full Frame) by changing a modular rear element.
-- This is a good for rental companies, who can use the same lens to service productions shot in different formats.
-- As the sensor size gets bigger, the focal length increases, and the wide-open aperture closes down.
-- As depicted below, each format requires a different rear element, iris ring, zoom ring and focus ring.
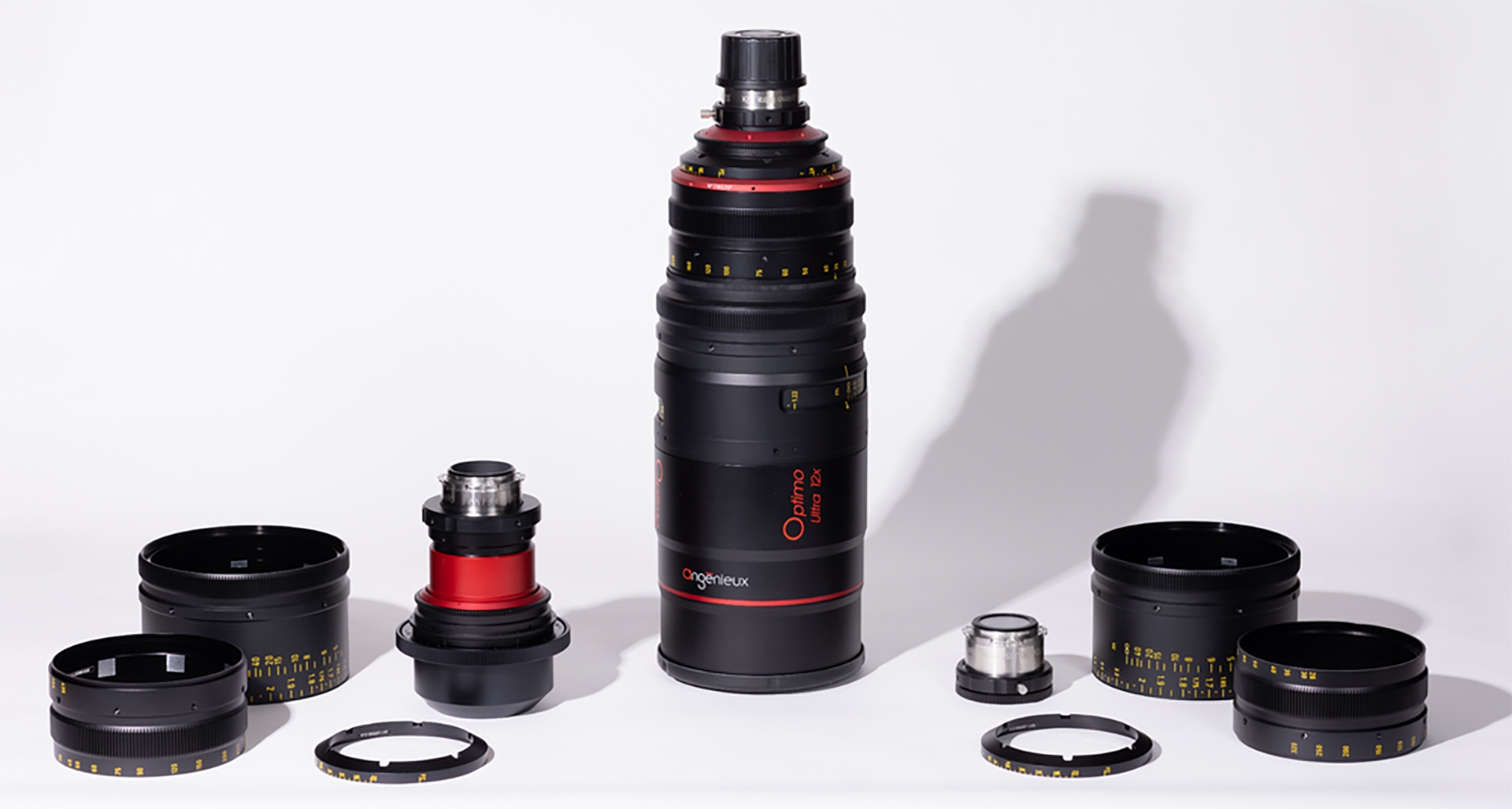
IOP = INTEGRATED OPTICAL PALETTE
After decades of zoom manufacture, Angénieux recently introduced a set of 12 Primes running from 18 to 200mm.
IOP refers to 3 possibilities for modifying the look of the lens, from lens front to back:
1- by inserting an internal glass filter
2- by changing the iris module to one with different blade configuration
3- by adding a rear filter (a traditional method)
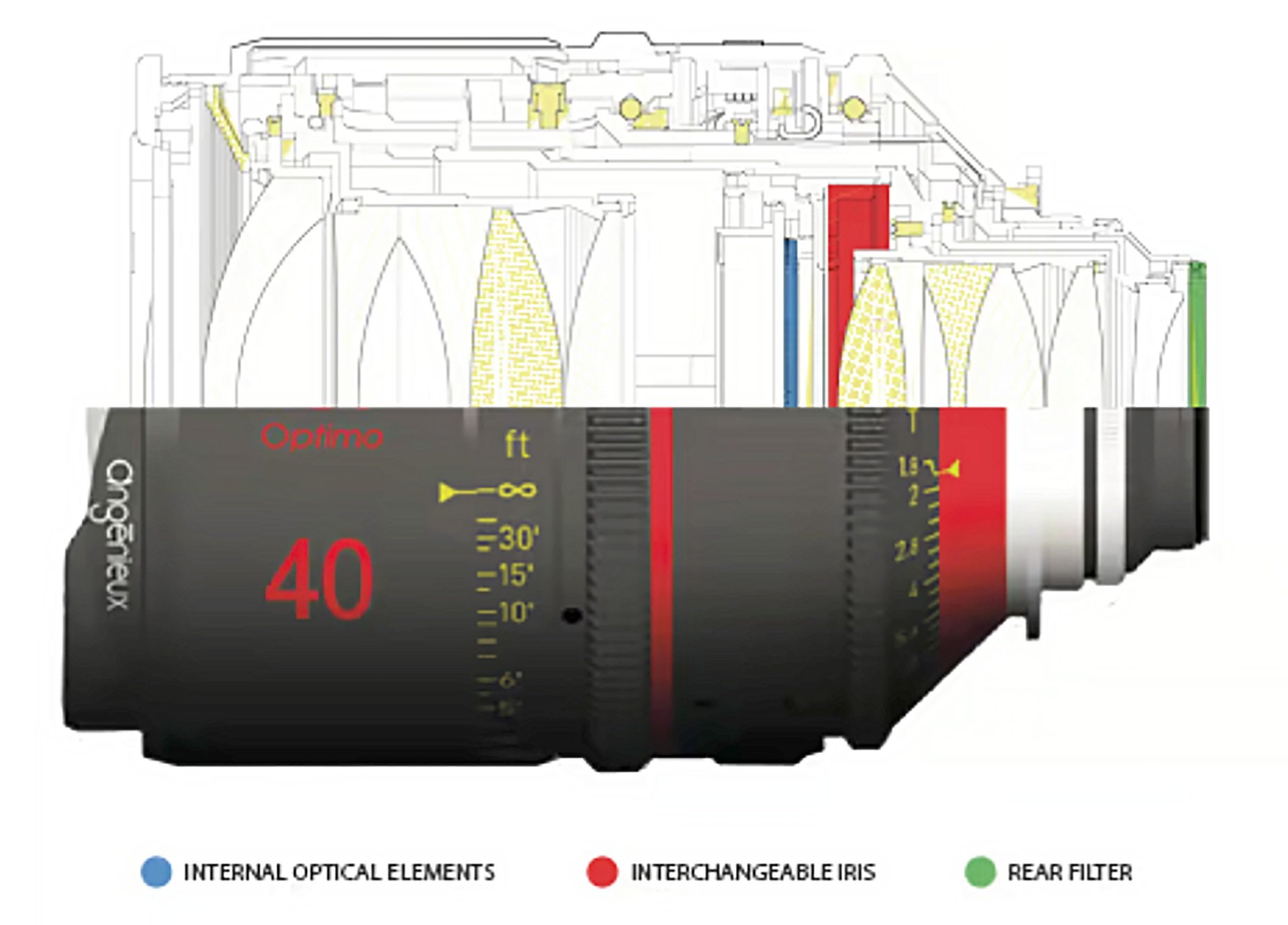
This modular approach addresses the desire of some cinematographers to work with “tunable” lenses to obtain a personal look.
-- Different iris shapes will create different bokeh shapes for highlights in the image, including pseudo-anamorphic ellipses
-- The afocal position of the internal filter should yield the same diffusion effect for all focal lengths, unlike front diffusion filters.
-- The growing list of available internal filters include Glimmer-glass, Black Satin, Black Pro-Mist and Low Contrast from Tiffen; and Hollywood Black Magic and Blue Streak from Schneider.
-- A clear glass filter can be tinted, sprayed, scratched or otherwise personalized for a unique look.
THE CAM
Vincent Collin, who heads the mechanical and optical workshops, is our first guide inside the factory. He presents a sculptural cross-section of an Optimo 24-290mm zoom. The dark tunnel at the center creates a room for the zoom's moving lens elements:
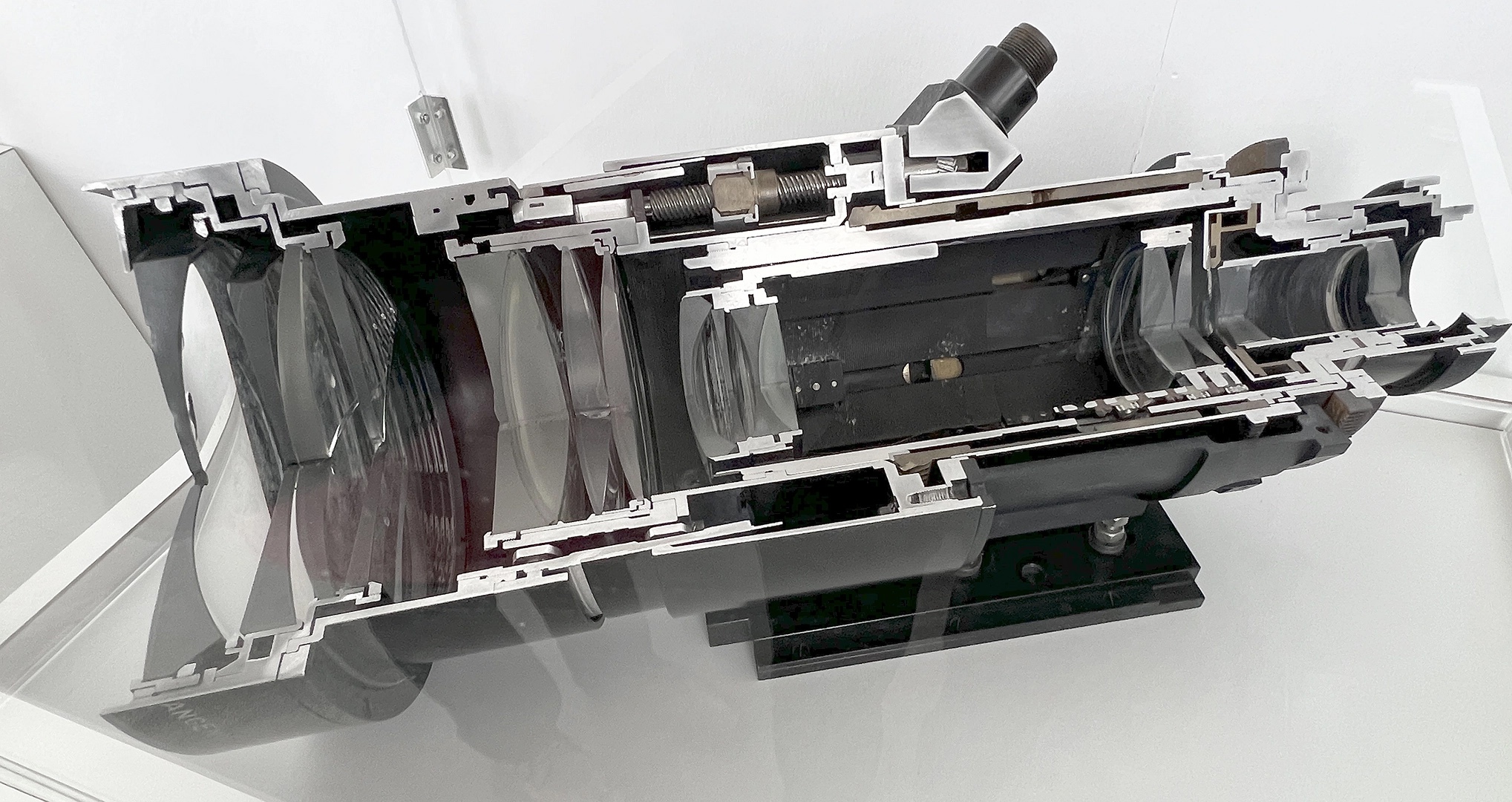
Every camera person is used to rotating the focus or zoom ring on the outside of a lens. This external rotation is mechanically transformed into an internal straight-line movement of lens elements along the lens axis, by means of a Cam with a groove.
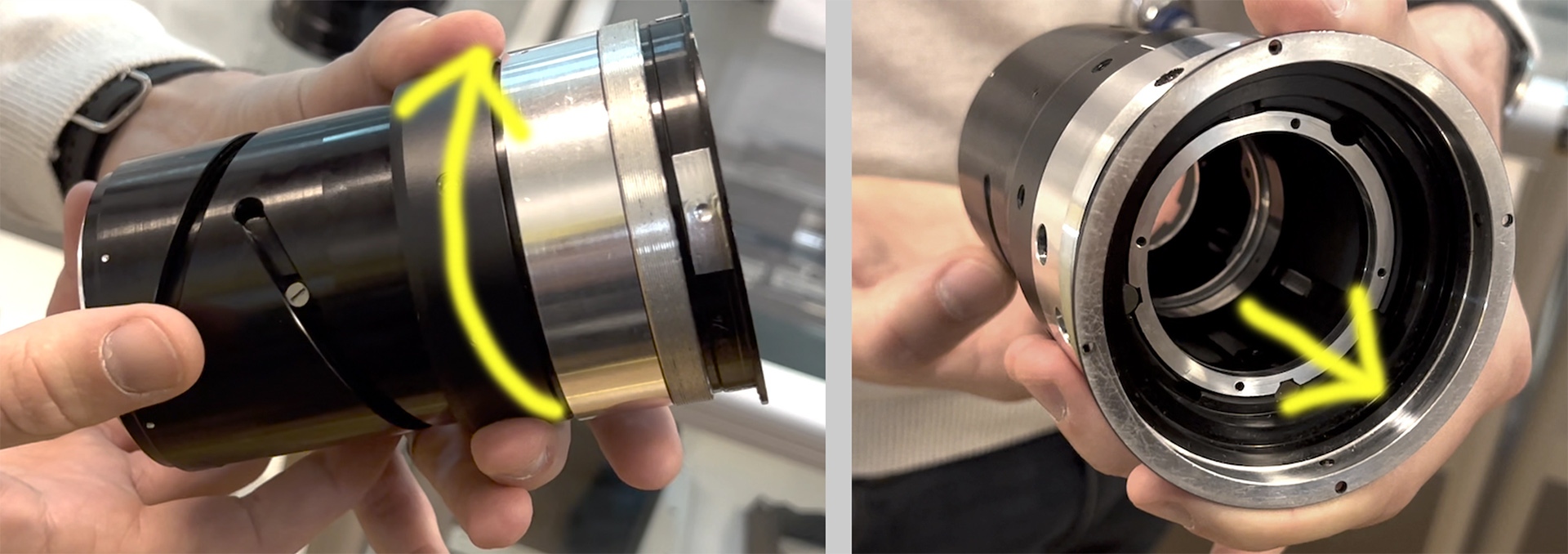
Vincent Collin then presents the zoom cam for the 12x Optimo, explaining that the precision of the groove is essential to the quality of the lens.
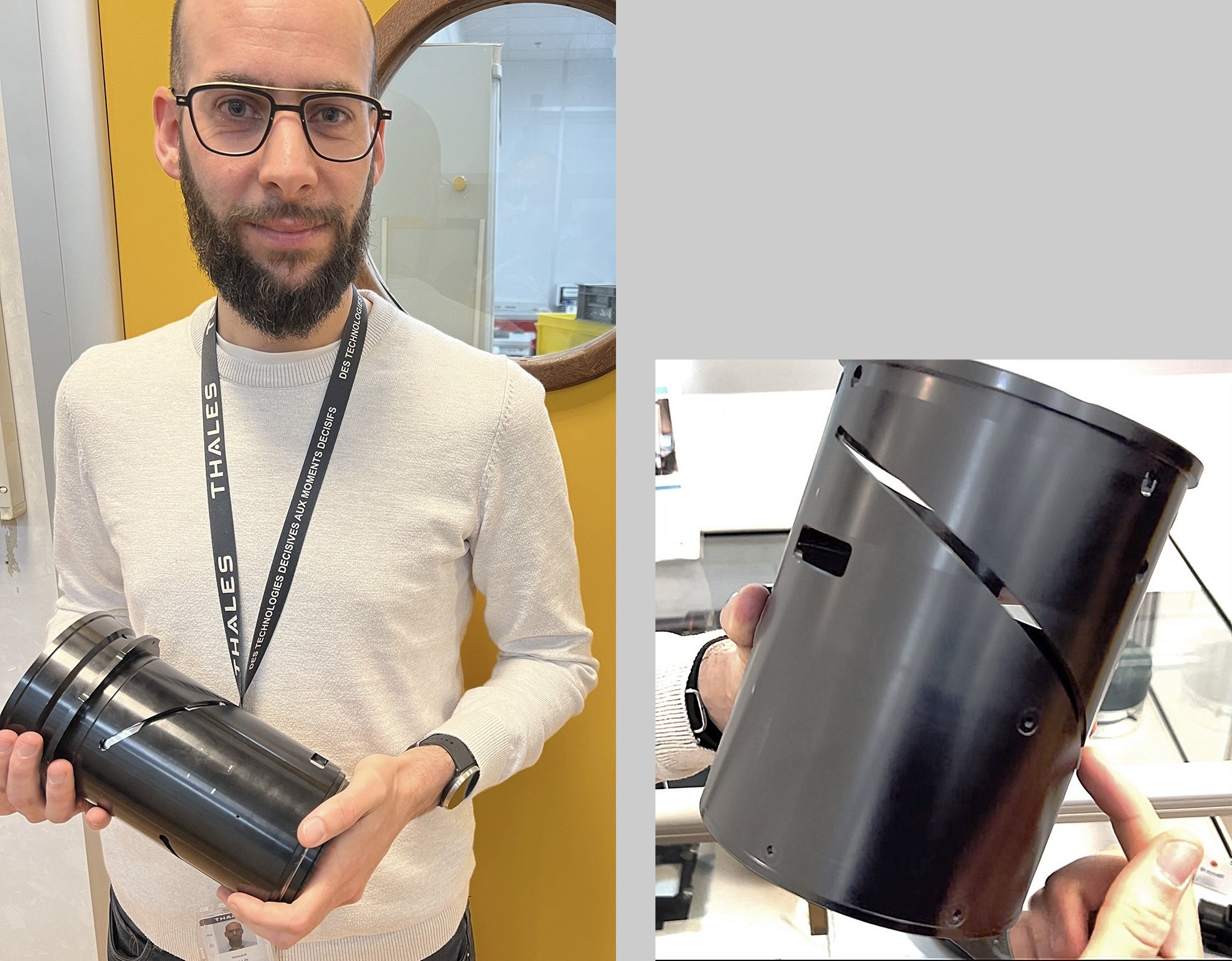
-- The Cams are manufactured on CNC (Computerized Numerical Control) machines, software-controlled systems with an array of tools to cut and fashion metal parts.
-- The Cam groove has an ultra-precise 1-micron tolerance, for accuracy and to avoid play as the zoom changes focal lengths
-- Cam precision is key, but so is repeatability. Each finished lens is physically zoomed between 500 to 1000 times before release, to “break in” the mechanical parts.
-- Aluminum is used for thermal stability
CNC MACHINE SHOP
We must don safety shoes before entering the machine shop, to protect our feet from heavy objects.
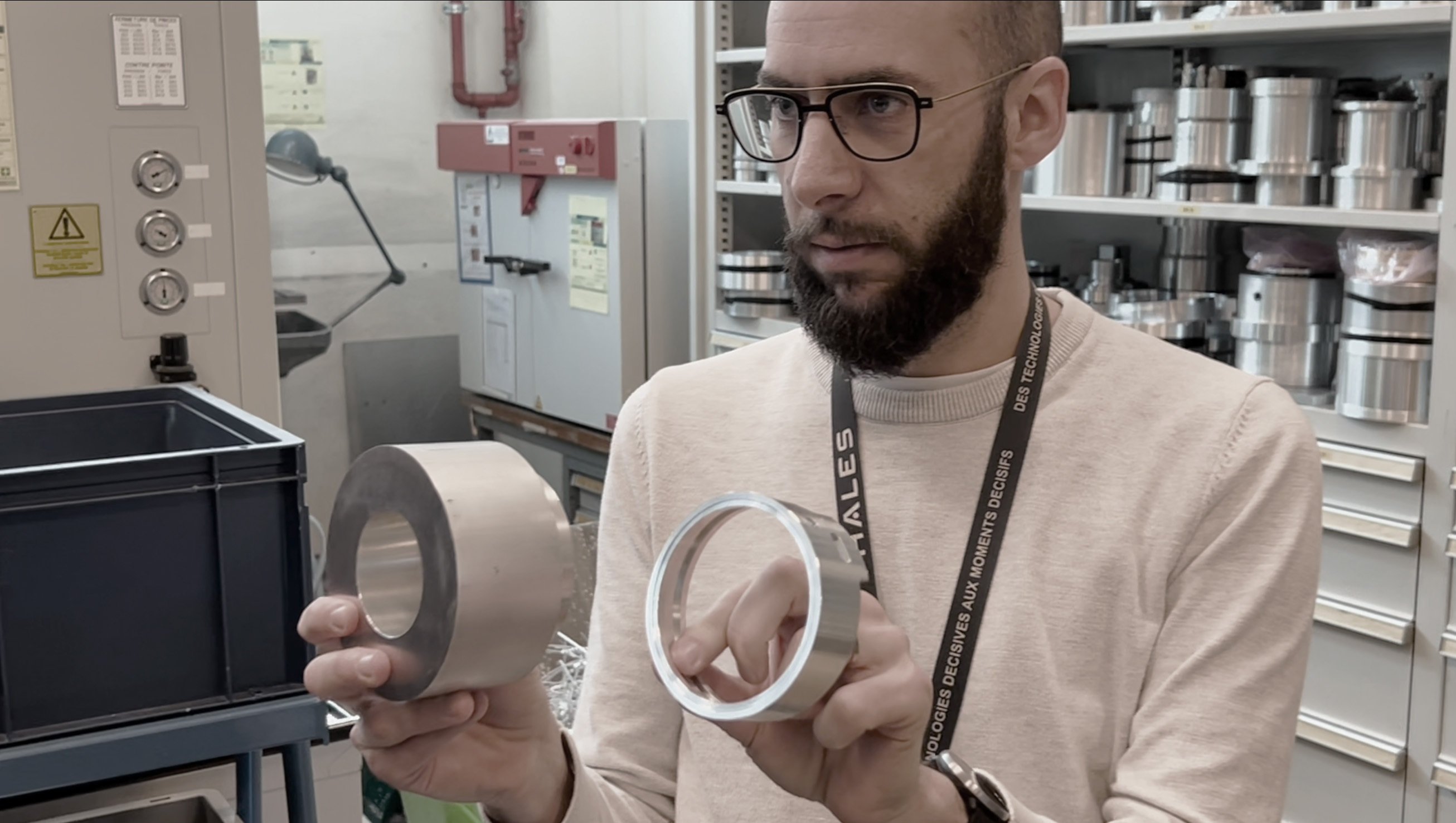
Vincent shows us a cylindrical block of aluminum and the focusing cam for their new 17-102mm zoom, which was carved out of a cylinder in 20 minutes by the many cutting and shaping tools in the CNC machine.
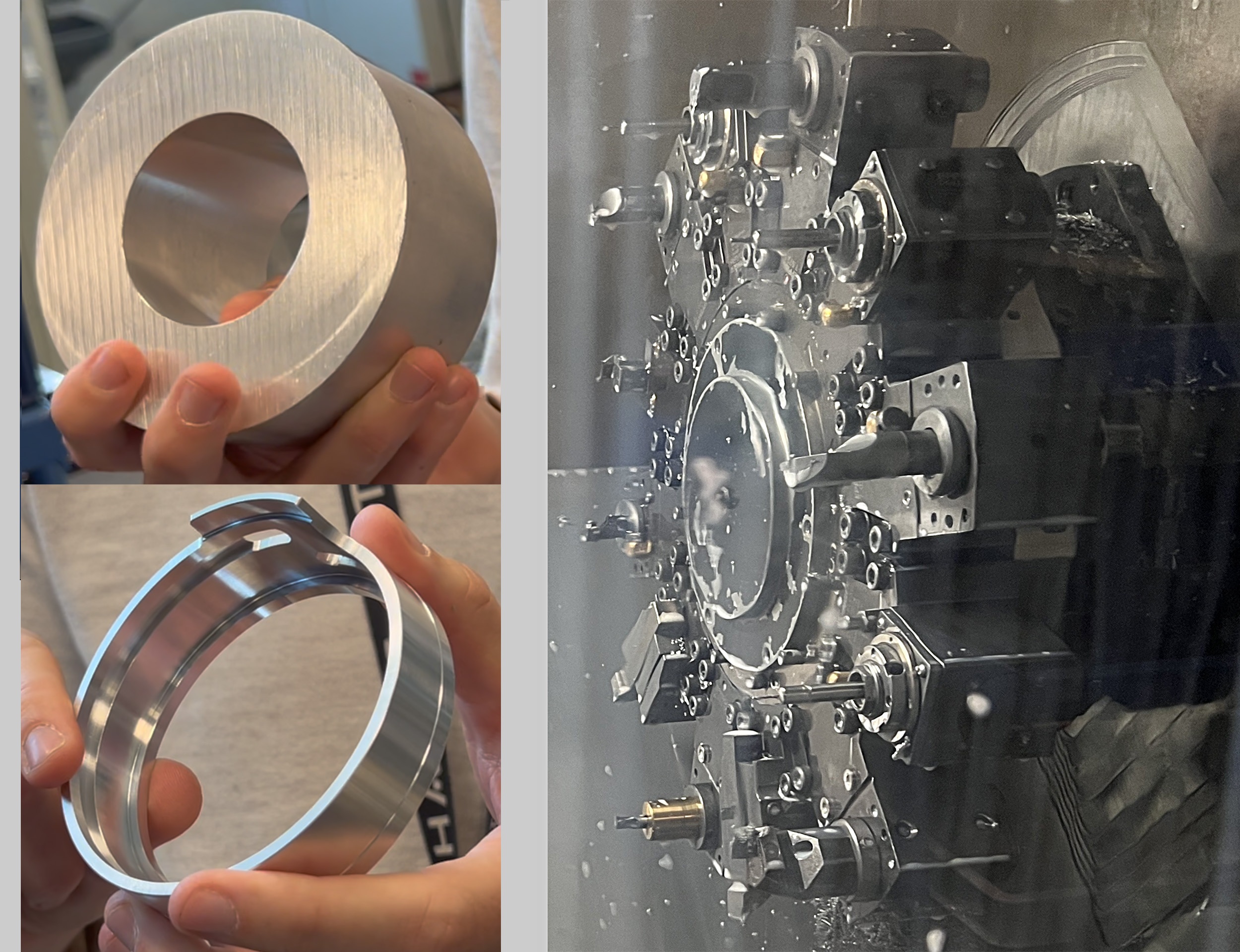
Distance marks on the lenses’ external focusing rings are cut by a diamond tip in a laser-assisted CNC machine.
-- The tolerance there is the mark width, about 1/10 of a millimeter.
-- Focus rings are not interchangeable; each is uniquely tailored to its lens.
-- The mechanical parts and lenses are put together in sub-assembly components before the final assembly.
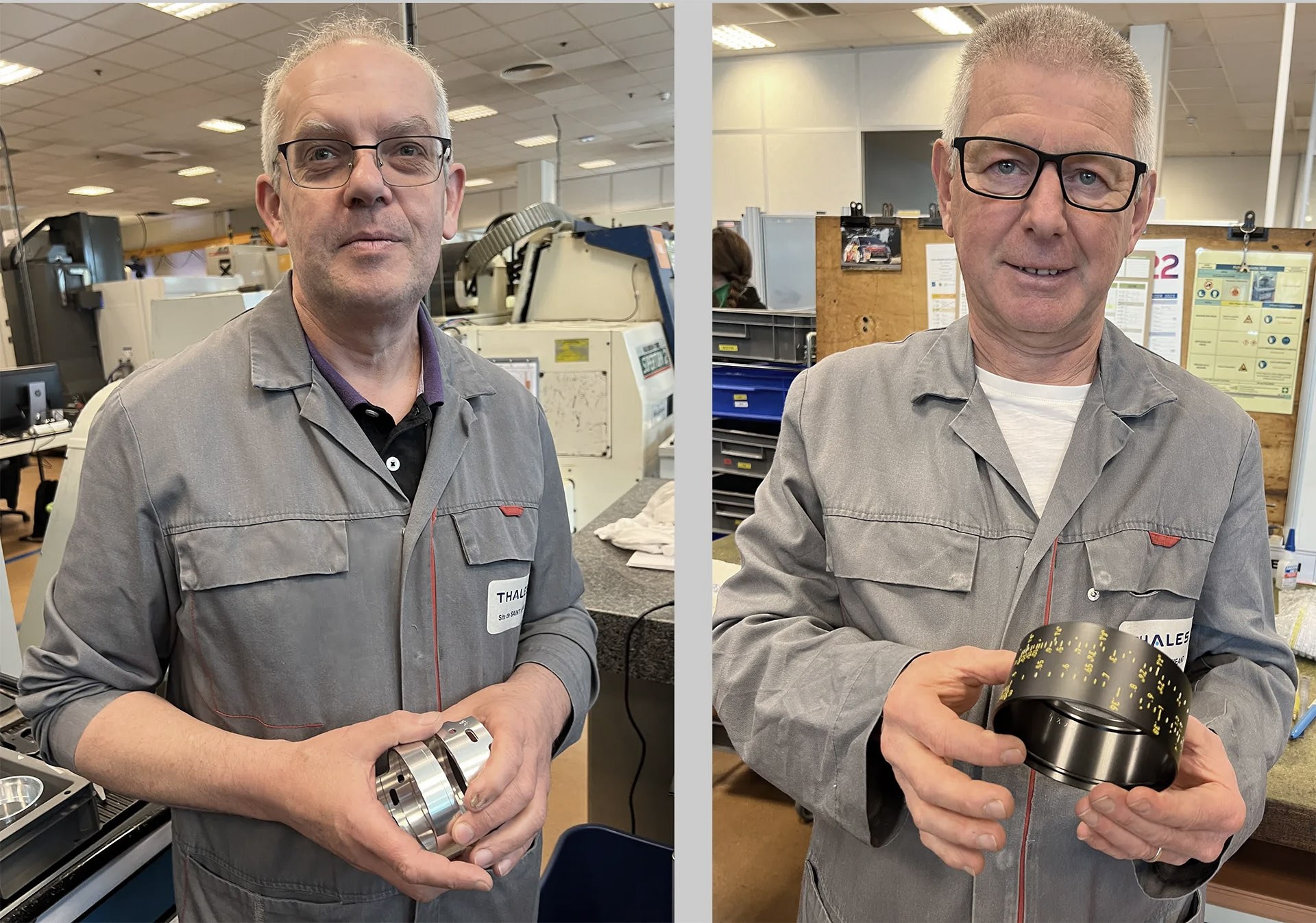
GLASS MACHINE SHOP
Vincent Collin continues our tour in the Glass machining and polishing workshop area.
-- Some lens elements are outsourced, but the most complex ones are finished in-house
-- Some glass arrives in circular cylinder blocks, with roughly ground surfaces
-- The final grinding in factory includes complex “aspheric” elements whose modulated surfaces are not evenly spherical.
-- Vincent says that the heart of the glass is better quality than the outlying parts, “like Comté cheese”. And indeed, the glasses look like cheeses!

Vincent shows us the raw glass and an abrasive fixture made of brass laced with diamonds that can shape and polish a lens element.
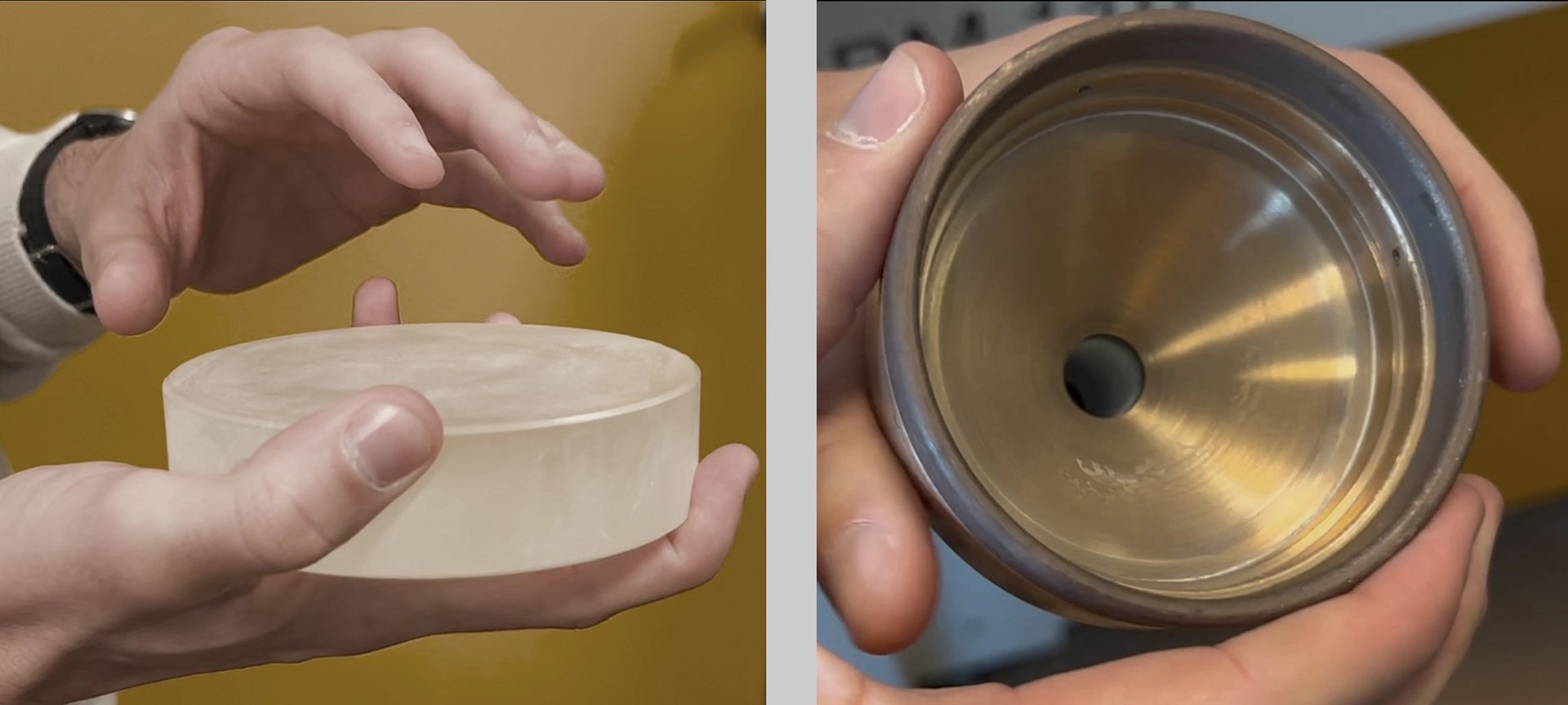
Vincent presents a CNC polishing machine, and his hands indicate the glass element above and the polyurethane polishing surface below, which will tilt to define the lens as the two rotating materials rub against each other.
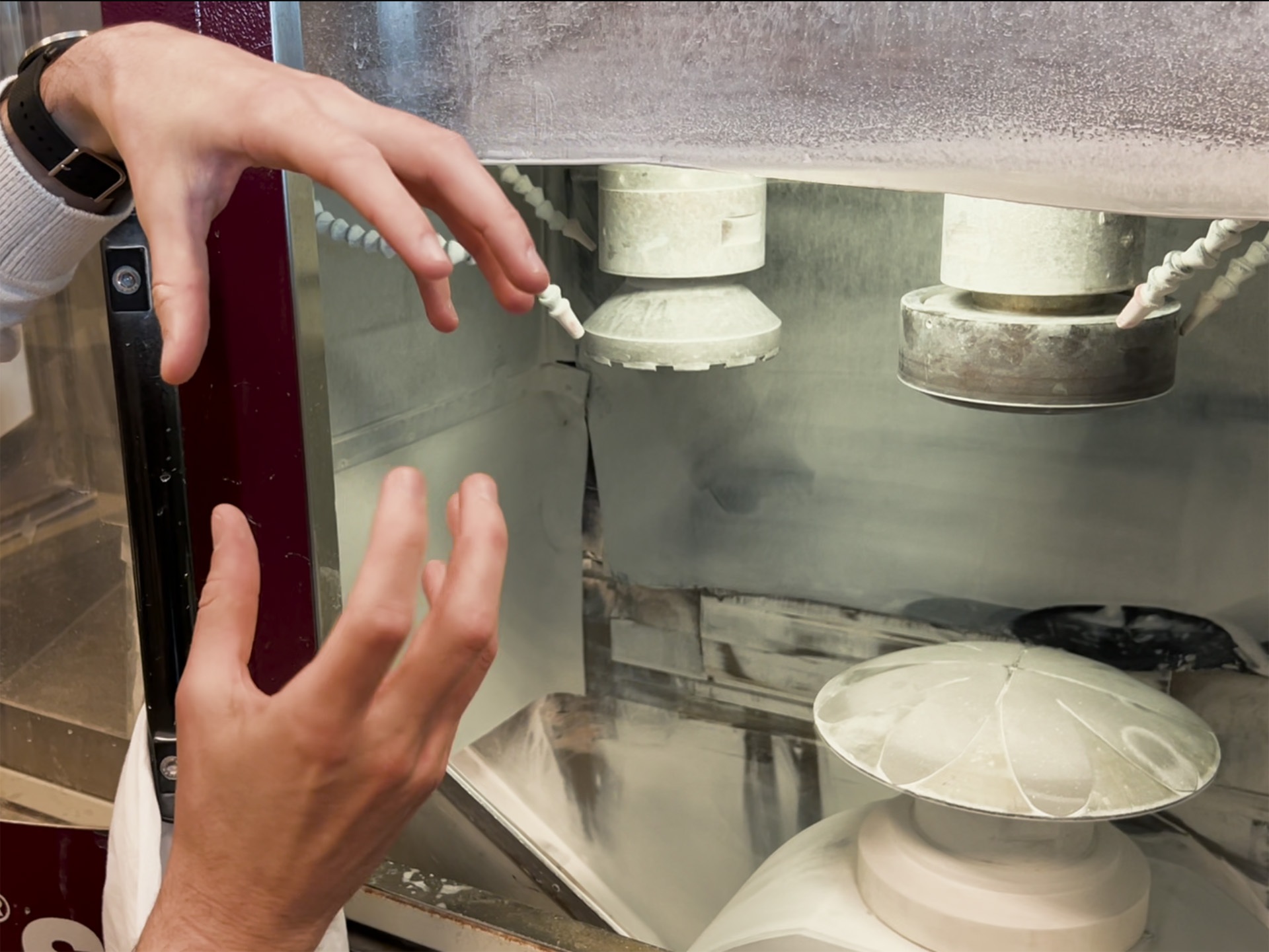
The case below contains a lens element before and after polishing. They appear black because their backings are covered in varnish and plastic for protection in the CNC machine.
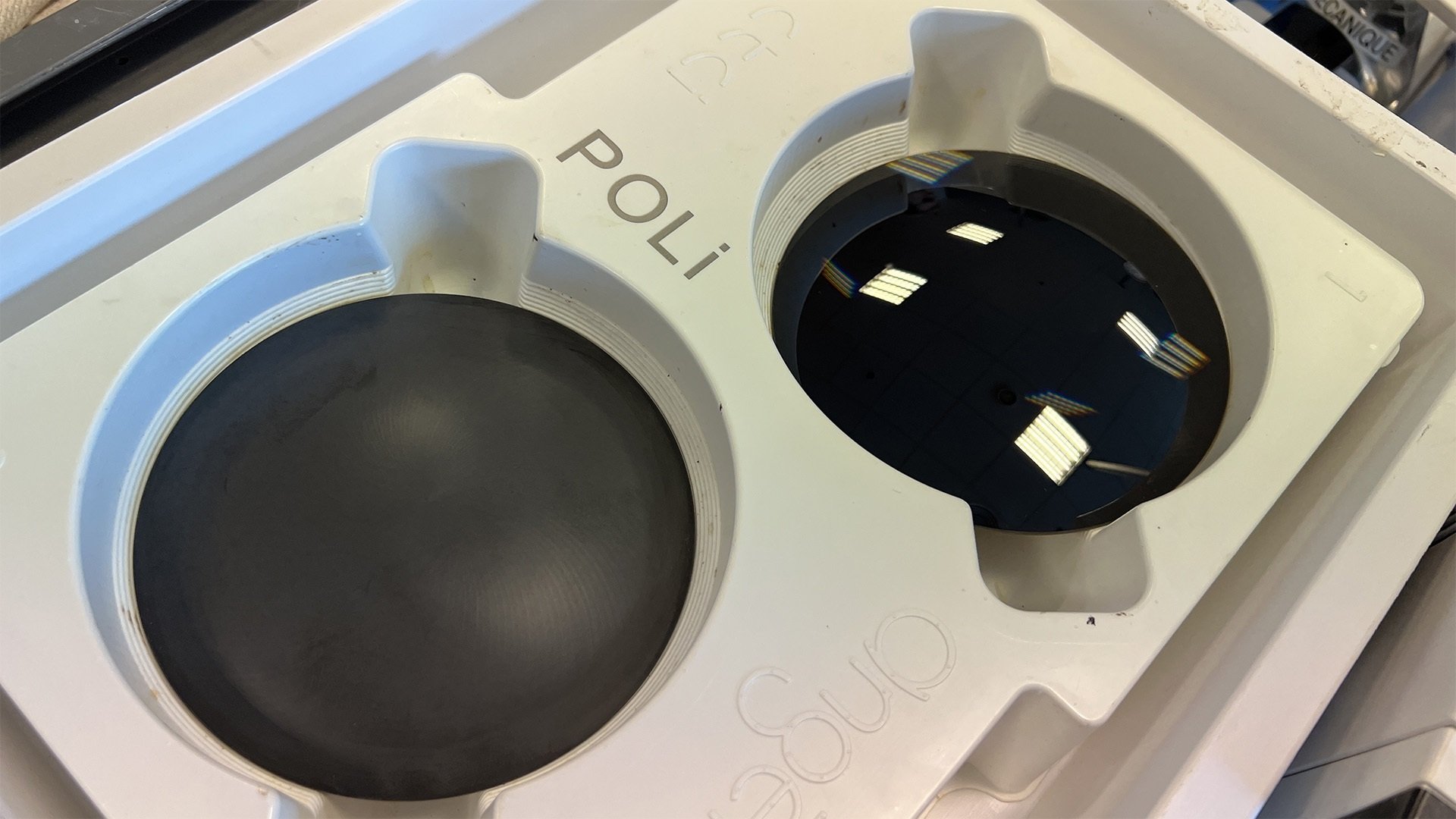
Some polished lenses are measured on an interferometer, a device that uses lasers to detect and measure microscopic flaws. The screen below displays a color-coded map of the lens where reds are the highest surfaces and blue the lowest. In this example the range from valley to crest is an astonishing 300 nanometers, or billionths of a meter. This digital map can then be used to improve the lens.
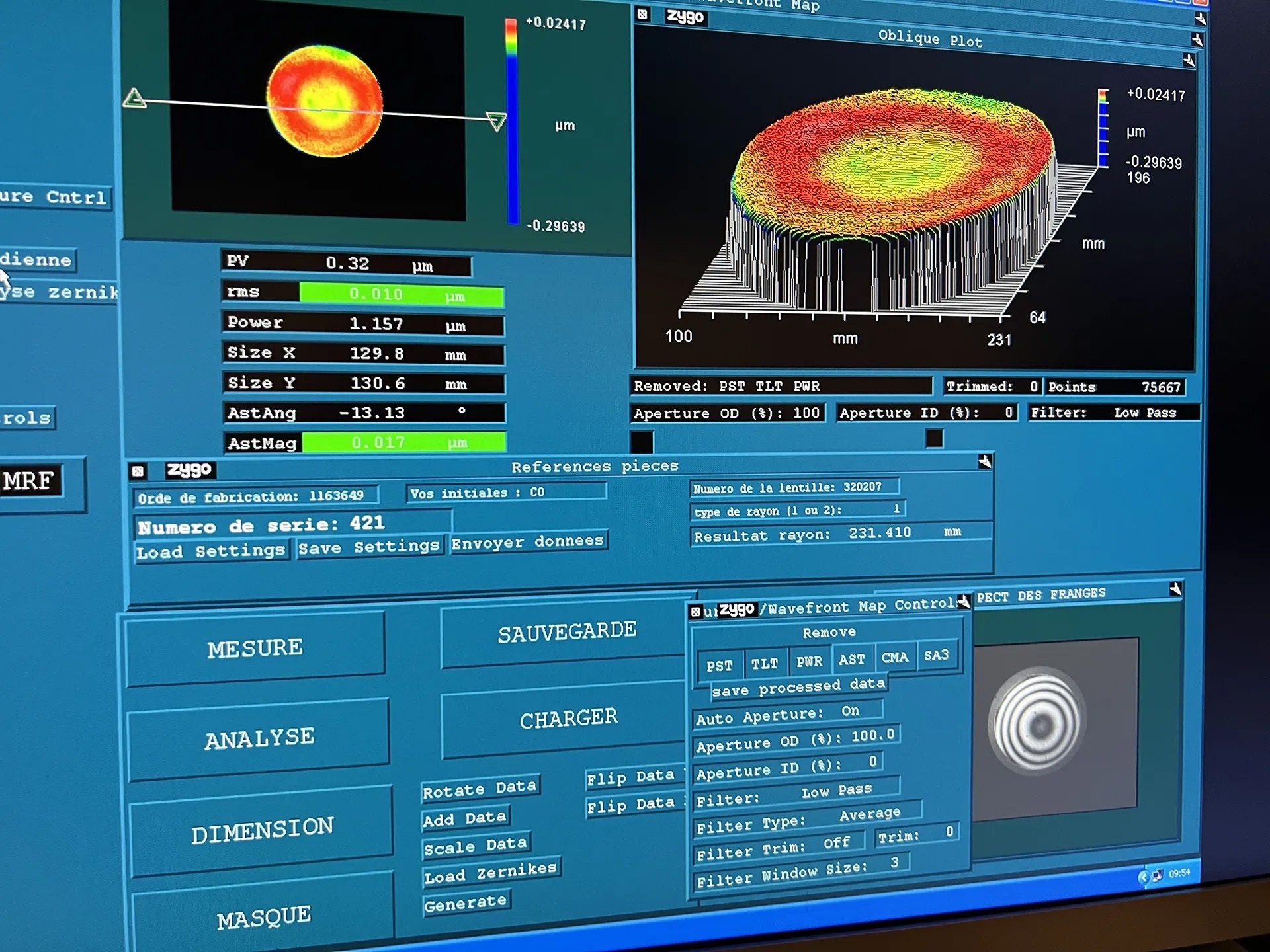
Below is a close-up view of a MRF (Magneto Rheological Finishing) machine which will, when possible, modify a small area of the glass surface, to improve a flaw. MRF uses a “smart fluid” laced with magnetic material, which can become a quasi-solid in a magnetic field. A similar process can be used to create an aspheric lens element, which has modulated curvature along its surface.
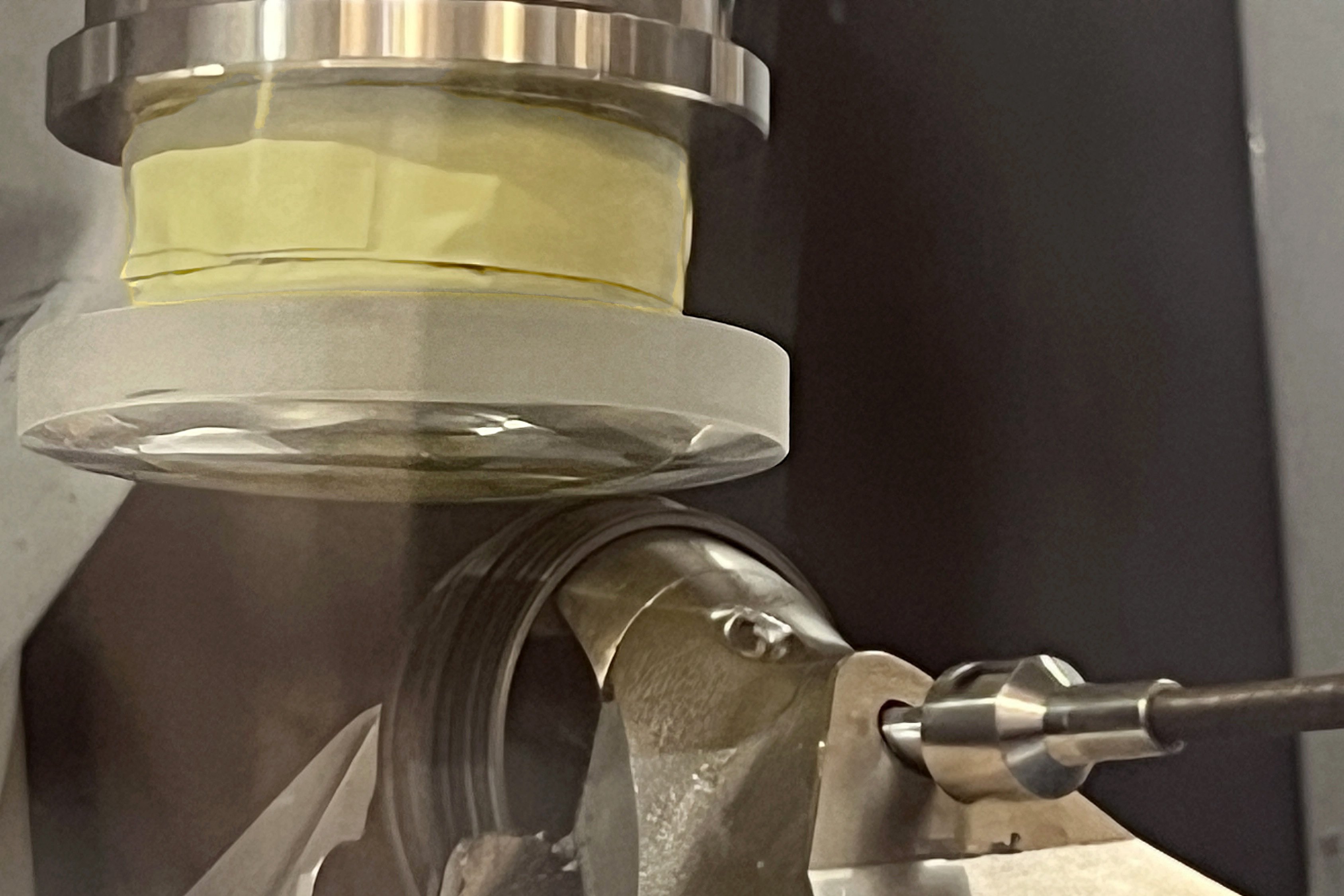
COATINGS AND VARNISH
Vincent Collin concludes his part of the tour by speaking of coatings and varnish.
-- He states that in an uncoated lens, as little as 8% of the light entering the front reaches the sensor at the rear, because of light reflections inside. Anti-flare coatings, "like those on our glasses," greatly reduce the light loss.
-- The PVD (Physical Vapor Deposition) coating machine is extremely high tech. It creates a near vaccum with zero dust.
-- An electron beam creates extreme heat (more than 200 degrees Celsius) to turn solid coating materials into gases that condense on the surface of the lens, "just like the condensation on your tea kettle lid," where they solidify.
-- Several coatings are applied with an extreme precision of "about 100 nanometers" (billionths of a meter).
-- Christophe Remontet notes that the coatings have a lot to do with the warm coloring of the lens.
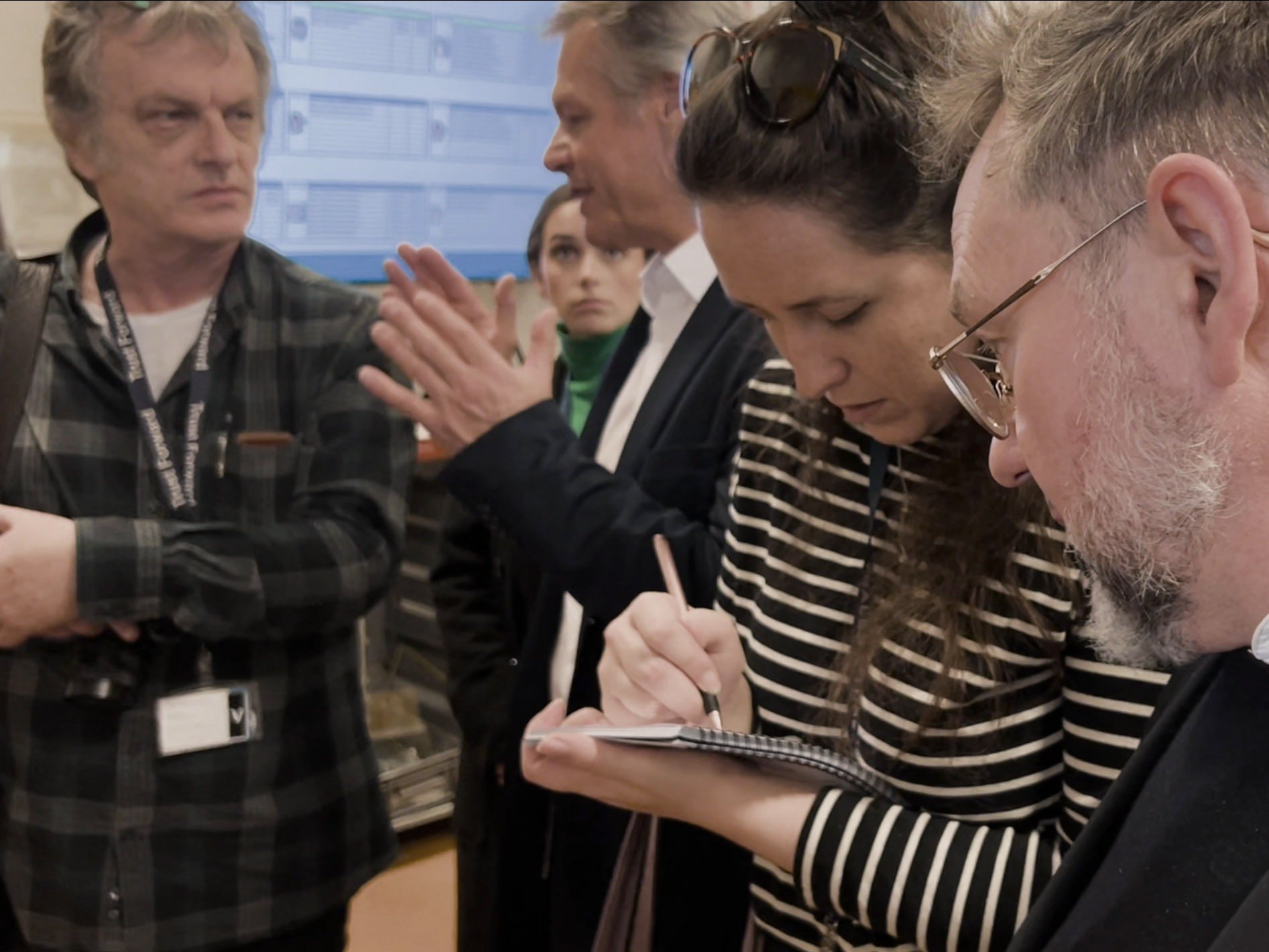
Vincent adds that black varnish is added to the materials surrounding the optical elements to reduce internal reflections.
-- The varnish is added by hand with a paint brush, with tolerances of fractions of a millimeter.
-- From nanometers to millimeters, the coatings and varnish are another example, says Dominique Rouchon, of the mixture of high tech and high craftmanship required to build a zoom.
LENS ASSEMBLY WORKSHOP
After thanking Vincent, our group is outfitted with light lab coats, to minimize dust contamination as we head into the Lens Assembly workshop, headed by Yvan Fournier.
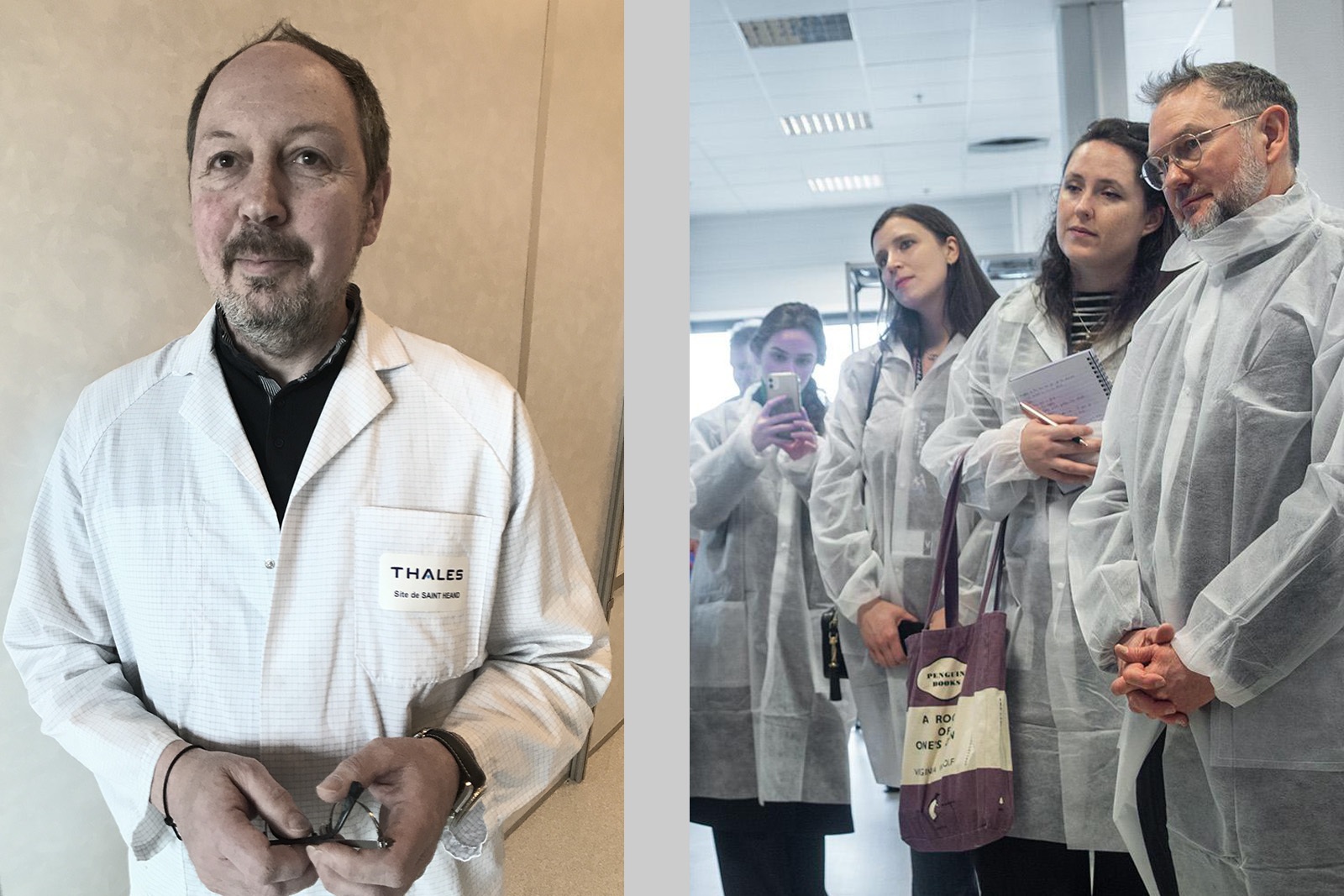
Yvan tells us that the workshop builds zooms and, in the past two years, primes.
-- A zoom can have as many as 24 lens elements and 500 mechanical elements. There are two workshops for sub-assemblies which are then assembled, adjusted, tested and finished in the final product.
-- Optical sub-assemblies are assembled and tested in a darkened room with bright spots to highlight dust and imperfections. There is also a device to check the centering and tilt of the combined elements.
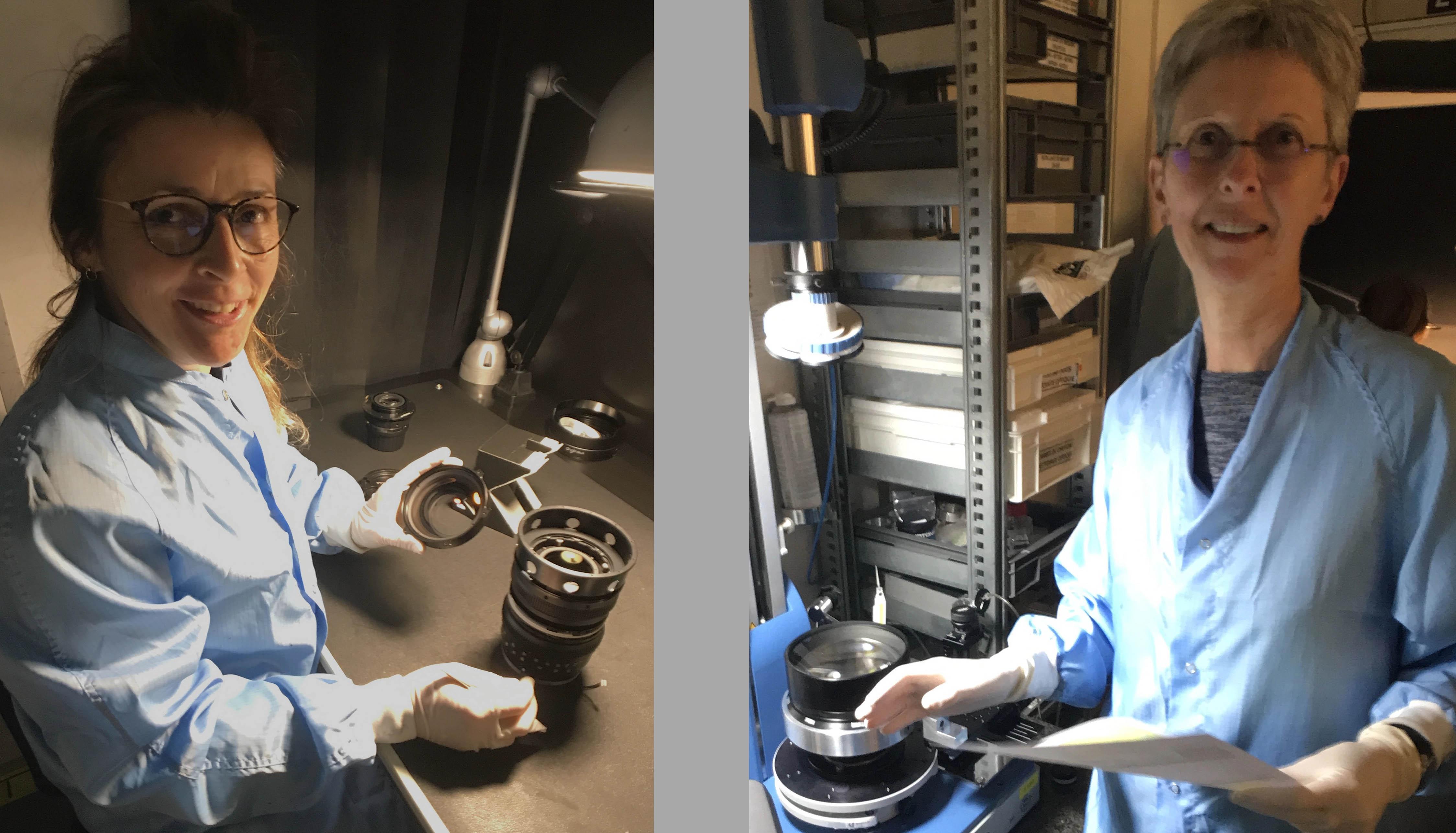
Lens assembly requires diligence and precision.
The workshop also does repairs.
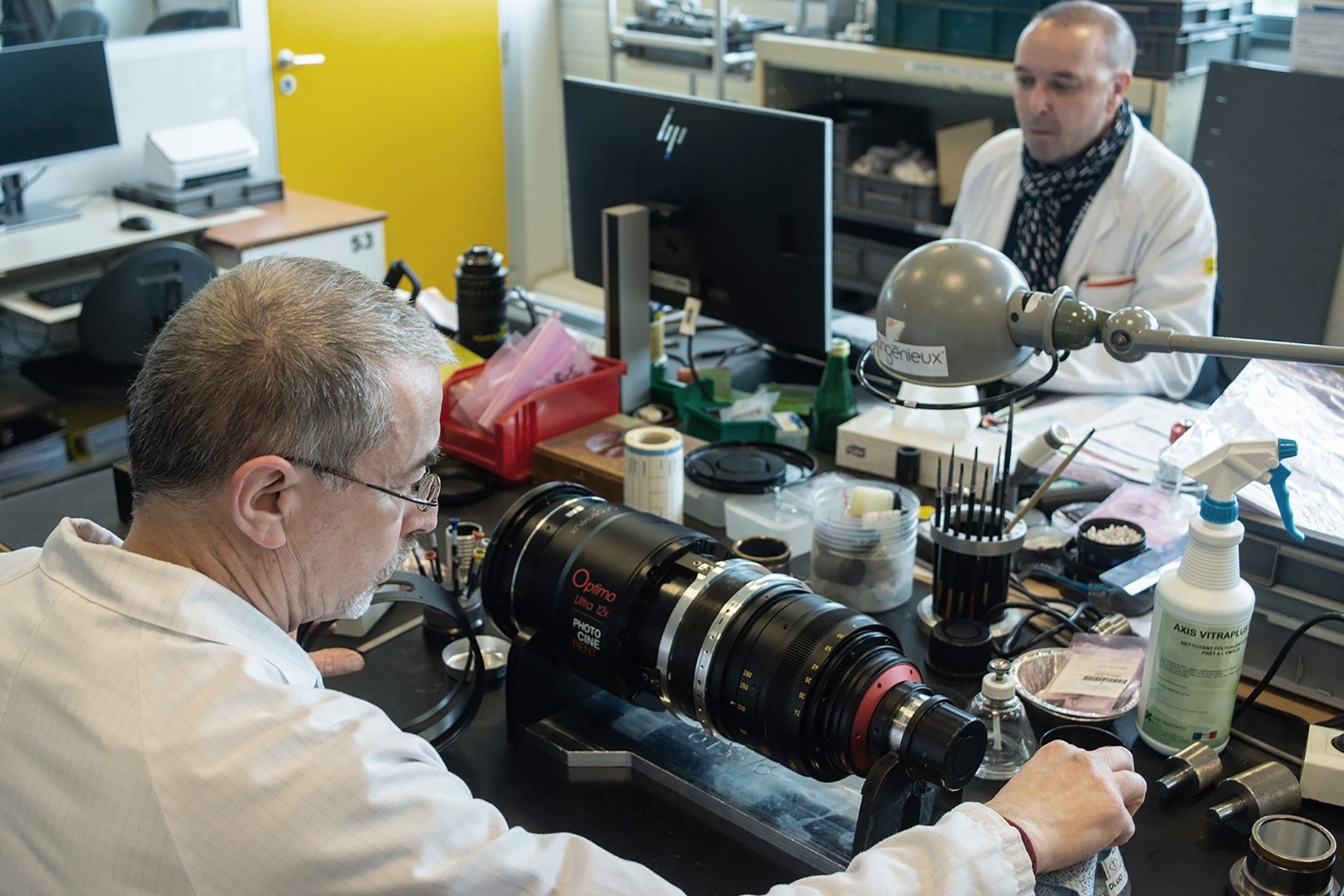
The finished lenses are checked in a dark room, by projecting a chart on a reticle through the back of the lens. The lens is examined at different focal lengths for homogeneity across the frame, and for spherical and chromatic aberrations.
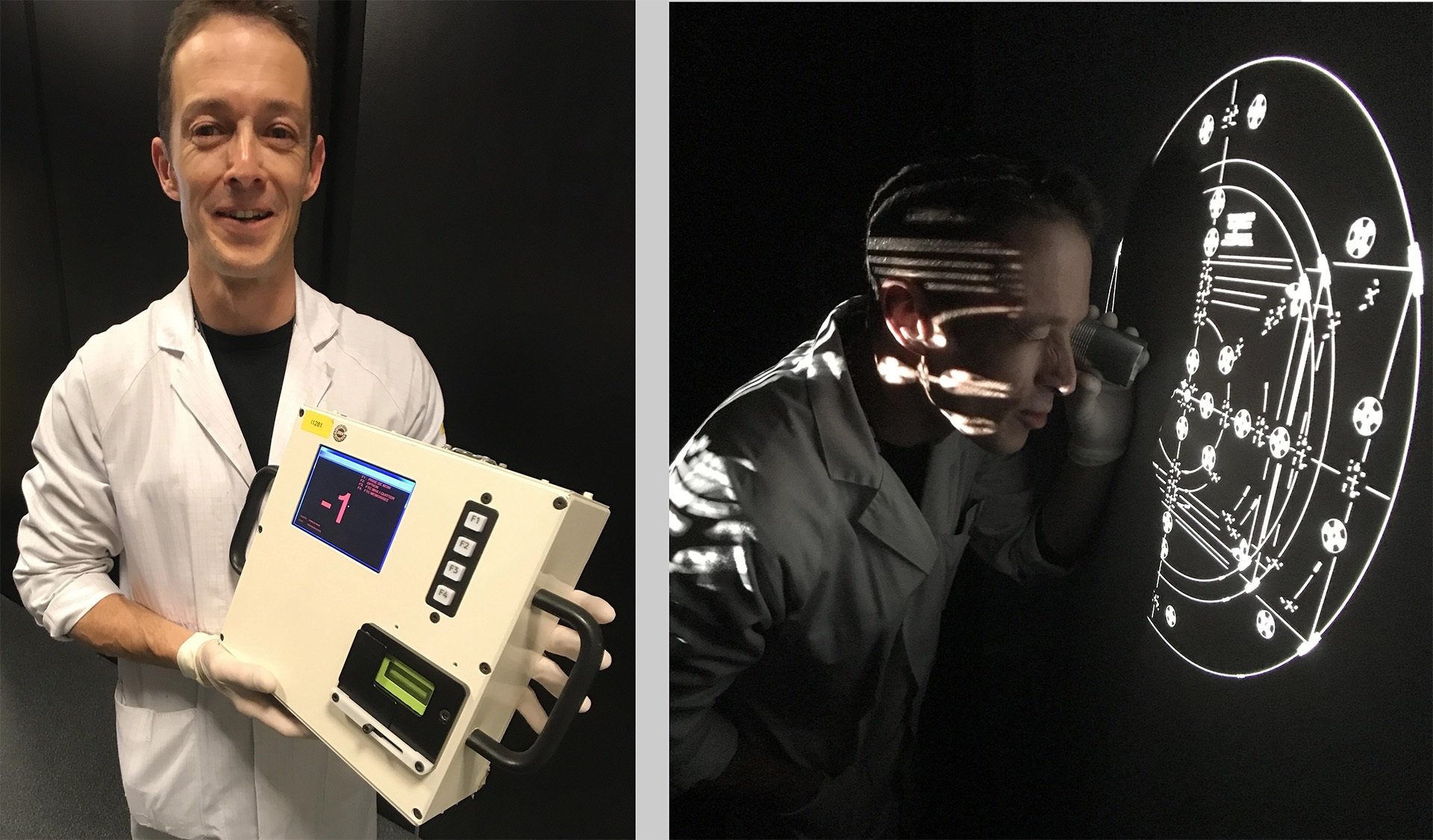
The quality of the lens is measured and evaluated by a practiced eye.
-- Yvan says that they check "up to 200 cycles per mm", representing "about 5 microns on the sensor." Checking focus at long focal lengths requires a magnifying glass.
-- The technicians also measure MTF (Modulation Transfer Function), an objective measure of contrast at different frequencies, using a very handy custom unit that quickly snaps on to the magnetic screen.
-- Just as important is the impression for a practiced eye of the lens' sharpness, clean image, color, bokeh and other subjective qualities at the appreciation of the cinematographer.
And indeed, the best way for a cinematographer to get to know a lens is to shoot with it on a project!
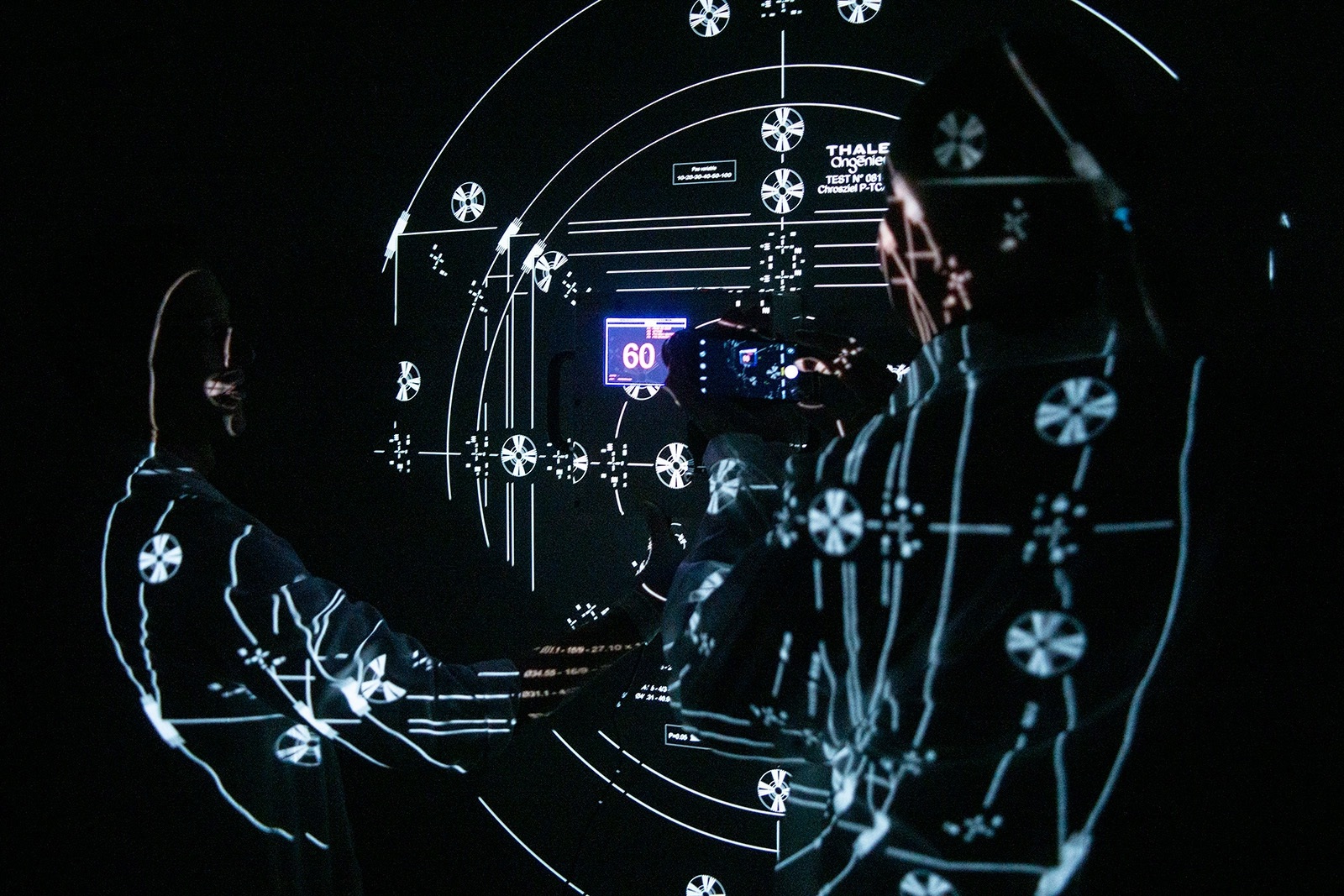
UN GRAND MERCI TO THE TEAM
I want to give a big "MERCI" to everyone we encountered at Angénieux, to our genial hosts Dominique Rouchon and Christophe Remontet, as well as to the support team for our visit.
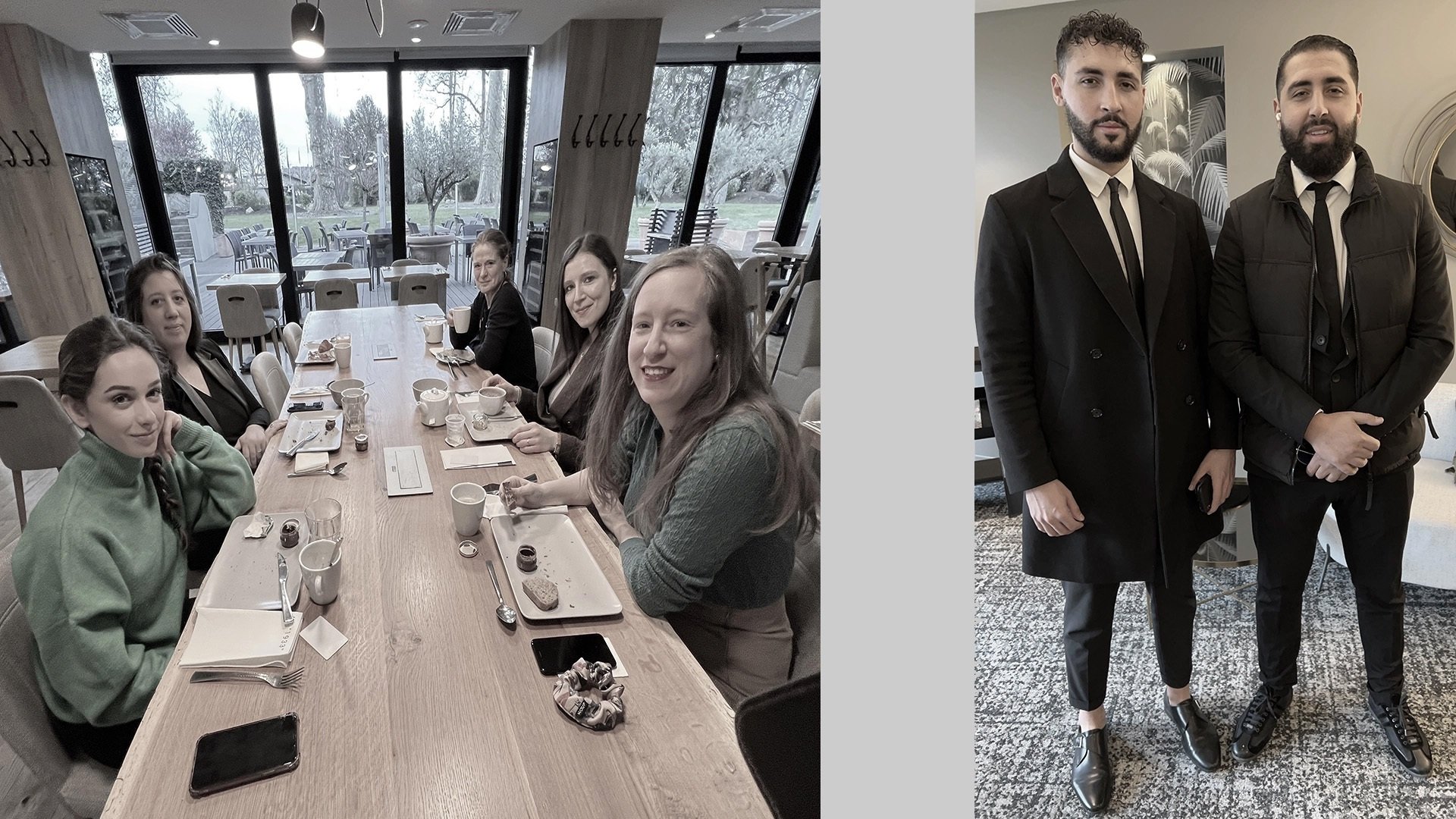
Unless otherwise indicated, all photos are © Benjamin B, 2023
Marc's photos © Marc Salomon, 2023
Angénieux photo Copyright Thales – CAPA Pictures